

Centra obróbkowe przygotowane do obsługiwania przez robot przemysłowy IRb-60 obróbki skrawaniem zestawu detali
Rozdział V. Badania modelowe i symulacyjne urządzeń:
W wyżej postawionym temacie przeprowadzono:
- badania modelowe w zakresie konstrukcji chwytaka elektromagnetycznego do pobierania i przenoszenia odlewa o największych gabarytach (najcięższego), mianowicie kadłuba WK - 1,3,
- badania modelowe w celu sprawdzenia namagnesowania się kadłuba w chwytaku z elektromagnesem,
- badania symulacyjne stolika pozycjonującego i układu orientująco-pozycjonującego.
Rozdział VI. Wybór koncepcji struktury w aspekcie funkcjonalnym, opracowanie struktury sprzętowej układu sterowania gniazda obróbczego
1. Wybór koncepcji struktury w aspekcie funkcjonalnym
Zadanie syntezy jest na tyle wieloaspektowe i złożone, że uzasadnione jest stosowanie przy jego rozwiązywaniu niektórych pojęć i metod teorii systemów.
Rozpatrywane gniazdo obróbcze stanowi system umiejscowiony w hierarchiach: technicznej i społecznej. Spośród aspektów badania systemowego, technicznego, ekonomicznego, socjalnego i ekologicznego, obszar dalszych rozważań będzie ograniczony, zgodnie ze zleceniem, do aspektu technicznego z elementami ekonomicznego. Uwzględnione zostaną podstawowe elementy pojęcia systemu, tj. jego cel, struktura, funkcjonowanie i ewolucja.
Zasadnicze założenia struktury i funkcjonowania gniazda obróbczego zostały określone, a część z nich szczegółowo opracowana i wykonana w ramach pracy [24]. Sprecyzowanie i wykonanie dalszych zadań, z uwzględnieniem czynnika ewolucji systemu, tj. niezbędnych zmian wynikających z ciągłego postępu naukowo-technicznego, wymaga usystematyzowania związanych z tym pojęć.
Na rys. 9 przedstawiono ogólną strukturę funkcjonalną gniazda obróbczego jako układu sterowanego. Wyodrębniono podstawowe bloki (układy) funkcjonalne: wykonawczy, zasilania, zbierania i wstępnego przetwarzania informacji, sterowania i układ komunikacji zewnętrznej, jakie można wyróżnić w każdym układzie sterowanym [29]. Ukazano także wejściowe i wyjściowe strumienie informacyjne i materiałowe, którym przyporządkować można konkretną treść w rozpatrywanym gnieździe obróbczym:
- zadanie (programy dla sterowników obrabiarek i robota przemysłowego oraz dla komputera sterującego),
- zasilanie (energią, surowcami, materiałami i narzędziami),
- produkty użyteczny (obrobione korpusy) i uboczny (wióry i ewentualne zanieczyszczenie środowiska),
- sygnały komunikacji zewnętrznej (sterowanie ręczne, uzależnienie zewnętrzne, sygnalizacja robocza i awaryjna).
Rys. 9. Struktura funkcjonalna gniazda obróbczego
Objaśnienia:
→ e, m - strumienie materiałowe i energetyczne,
→ u, s, - strumienie informacji,
z - zadania (zadanie algorytmu funkcjonowania układu)
U, U1, U2 - sygnały sterowania ręcznego i uzależnień zewnętrznych,
s - sygnalizacja robocza i alarmowa,
e, m - energia i materiały,
p – produkty: użyteczny i uboczny
x1, x2, x3 - sygnały sterujące
y1, y2, y3 - sygnały sprężeń zwrotnych,
US - układ sterujący,
Z - układ zasilania energią i materiałami,
UW - układ wykonawczy,
Z i WPI - układ zbierania i wstępnego przetwarzania informacji,
K - układ komunikacji zewnętrznej.
Przyporządkowanie poszczególnym układom funkcjonalnym części fizycznych układu nie jest w pełni jednoznaczne ze względu na różnorodność funkcji niektórych spośród tych części. Tym niemniej celowe jest następujące przyporządkowanie, oparte na dekompozycji układu na poziomie jednostek sprzętowych zakupionych lub zaprojektowanych i wykonanych:
a) układ wykonawczy: centra obróbcze, część manipulacyjna robota, uchwyty obróbcze, odkurzacz przemysłowy, magazyn wyjściowy
b) układ zasilania:
- energią - zasilacze elektryczne i hydrauliczne centrów obróbczych, robota i uchwytów obróbczych,
- materiałami: palety / z odlewami do obróbki, magazyn narzędzi, zbiornik hydrauliczny czynnika roboczego.
c) układ zbierania i wstępnego przetwarzania informacji:
- w zakresie zbierania: czujniki stanu narzędzi i blokady przestrzeni roboczej, czujniki stanu pracy obrabiarek
- w zakresie wstępnego przetwarzania: interfejs czujników stanu narzędzi.
d) układ sterujący: mikrokomputer, szafa sterownicza robota przemysłowego, szafy sterownicze centrów obróbczych, sterownik bitowy.
e) układ komunikacji zewnętrznej:
- układ wejść: konsola operatora
- układ wyjść: sygnalizatory awaryjne stanu narzędzi, otwarcia przestrzeni roboczej, braku odlewów w palecie, niewykonanie poszczególnych partii programu przez robota, wyłączeń awaryjnych robota i obrabiarek; sygnalizatory robocze (stanu centrów obróbczych, robota przemysłowego, palety i magazynu wyjściowego.
Wymienione wyżej układy (bloki) funkcjonalne można zgrupować w dwa makrobloki: przetworzenia energii i materiałów zawierających bloki zasilania i wykonawczy (część energetyczna układu) oraz makroblok przetwarzania informacji i sterowania zawierający pozostałe bloki (część informacyjna układu(. W odniesieniu do tej drugiej części układu stosowana jest również nazwa układu steroWania. Przedmiotem rozważań niniejszego rozdziału jest właściwie układ sterowania w takim szerokim znaczeniu.
Blok sterujący (US na rys. 9) w układzie sterowania zarządza działaniem wszystkich pozostałych bloków układu, zapewniając realizację zadań. Treść tych zadań wynika z celu istnienia układu i określone jest przez strukturę i funkcjonowanie części energetycznej, natomiast ich forma jest pochodną budowy układu sterowania.
2. Struktura sprzętowa układu sterowania.
Struktura części energetycznej gniazda obróbczego bazuje na istniejących centrach obróbczych. Do ich zautomatyzowanej obsługi wybrano podczas realizacji pracy [24] robot przemysłowy IRb-60. Biorąc pod uwagę jego dane techniczne, był on wówczas i jest nadal najbardziej odpowiednim spośród robotów krajowej produkcji do realizacji postawionego zadania. Jednakże w obecnie dostępnej wersji, którą należy zaliczyć do robotów pierwszej generacji, ograniczone możliwości układu sterowania robota niekorzystnie rzutują na możliwości zaprojektowania i realizacji układu sterowania gniazda obróbczego. Roboty IRb posiadają sterowanie typu PTP (point-to—point, punktowe), a ich programowanie odbywa się metodą uczenia pośredniego (indirect teach - in). Układ sterowania robota nie posiada wbudowanego systemu przerwań i nie jest wyposażony w wejście sygnałów sterowania ruchami przez komputer zewnętrzny. Wprawdzie wejście takie jest zwykle niezbędne dopiero przy konieczności synchronizacji pracy wielu robotów, na wyższym szczeblu budowy elastycznego systemu produkcyjnego, jednakże w przypadku rozpatrywanego gniazda jest konieczne w przypadku obróbki korpusów CGŁ, a także w przypadku zastosowania stanowiska identyfikującego położenie detali w rozważonych procesach technologicznych przy warunkach określonych w rozdziale III.
Typowym rozwiązaniem podawania przedmiotów manipulacji tego rodzaju robotem jest poletyzacja (3, 37, 39, 40, 41). Autorzy proponują przyjęcie takiego właśnie rozwiązania (rozdział III).
W przypadku przyjęcia jednak wersji z identyfikacją przedmiotu rozwiązanie współpracy układu identyfikacji z układem sterowania robota należy ująć z uwzględnieniem ewolucji systemu.
Rozwiązanie docelowe powinno bazować na robocie drugiej generacji, którego układ sterowania posiada, jako minimum wymagań, moduł interfejsu szeregowego (np. V-24). Umożliwia to przyłączenie procesora zewnętrznego, przetwarzającego obraz „widziany” przez czujnik wizyjny i adaptacyjne sterowanie napędami części manipulacyjnej, umożliwiające pozycjonowanie obrabianego odlewu przez odpowiednie przemieszczenia i zorientowanie chwytaka. Ponadto jednostka centralna takiego układu sterowania robota mogłaby pełnie rolę jednostki centralnej (komputera nadrzędnego) całego układu sterowania gniazda obróbczego. Taki układ sterowania dla robotów IRb opracowano w Przemysłowym Instytucie Automatyki i Pomiarów [35], bazując na produkowanym przez Zakłady Automatyki Przemysłowej w Ostrowie Wielkopolskim zdecentralizowanym mikrokomputerowym systemie automatyki przemysłowej INTELDIGIT—PROWAY [31]. Istnieje teoretyczna możliwość rozszerzenia togo układu sterowania robota o moduł dodatkowego procesora służącego do przetwarzania obrazu, co pozwoliłoby zrezygnować z procesora zewnętrznego. Jednakże pierwsze roboty z tym układem sterowania będą wyprodukowane w 1988 roku, a portfel zamówień jest wypełniony co najmniej na rok (informacja uzyskana od przedstawicieli PIAP). W tej sytuacji celowe stałoby się wdrożenie do przetwarzania sygnałów czujnika wizyjnego zewnętrznego procesora, który mógłby współpracować z aktualnie stosowanym układem sterowania, umożliwiając przyszłą adaptację do systemu INTELBIGIT — PROWAY.
W pracy [24] przewidziano, uwzględniając ówczesne możliwości realizacyjne, zastosowanie jako procesora zewnętrznego minikomputera ZX-Spectrum. Układ sterowania gniazda obróbczego nie zawiera przy tym żadnej jednostki centralnej (komputera nadrzędnego), lecz poszczególne jego bloki kolejno wykonują swoje funkcje. Rozpoczęcie działania następnego bloku inicjowane jest przez zakończenie czynności poprzedniego bloku, bez możliwości przerwań. Zaletą tego rozwiązania, wynikającą z możliwości realizacji sprzętowej, jest to, że układ sterowania gniazda obróbczego znajduje się w końcowej fazie opracowania i w następnym etapie pracy można będzie przy jego pomocy przeprowadzić badania doświadczalne, których, wyniki będą znaczące także dla kolejnych modyfikacji układu, zawierających inny procesor. Wadą natomiast jest, że mikrokomputer ten z założenia nie był konstruowany pod kątem zastosowania do sterowania procesami przemysłowymi. Wynika z tego, że w przypadku dalszych prac badawczo-doświadczalnych zmierzających do nadania gniazdu struktury elastycznej jego pojemność pamięci może okazać się (z dużym prawdopodobieństwem) niewystarczająca. Poza tym urządzenie to wykazuje większą wrażliwość na zakłócenia niż specjalizowane układy mikroprocesorowe.
Jako pierwszą z modyfikacji proponuje się zastąpienie mikrokomputera ZX Spectrum przez procesor przystosowany do pracy w układach automatyki przemysłowej. Powinien on być przy tym modułem mikrokomputerowego systemu automatyki, co pozwoli w kolejnysh etapach automatyzacji obróbki korpusów wyeliminować stolik pozycjonujący, a następnie wykorzystać procesor jako jednostkę centralną układu sterowania gniazdem obróbczym.
Przy zastosowaniu robota IRb-60 drogą prowadzącą do przejścia przez robot funkcji pozycjonowania, a więc do eliminacji stolika pozycjonującego, może być symulacja sterowania ręcznego przez ten mikroprocesor.
Bibliografia: 1.techas@gmail.com
|
REKLAMA |
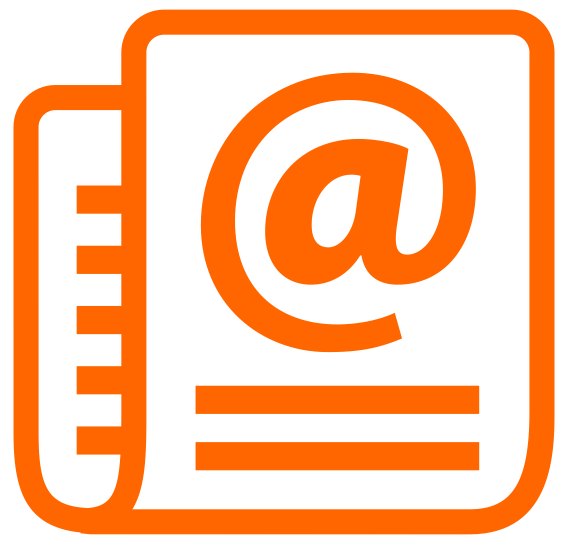
REKLAMA |
REKLAMA |
REKLAMA |
REKLAMA |
|
Łącza Radiowe i ... Łącza radiowe punkt-punkt, punkt-wielopunkt, Sieci dostępowe WiFi, Stacje Bazowe telefonij ... |
![]() |
|
Falowniki Informacje na temat elektrycznych systemów napędowych. |
![]() |
|
Po godzinach Po godzinach to miejsce odpoczynku, przeczytasz tu kawały, dowcipy,śmieszne historie i inne rzeczy ... |
![]() |
|
Koło naukowe programistów Koło naukowe poruszające zagadnienia związane z programowaniem w różnych językach: C/C++/C# , ... |
![]() |
REKLAMA |
Gość
17:12
13 kwiecień 2012
Kto dokonał zniszczenia:Centra obróbkowe przygotowane do obsługiwania przez robot przemysłowy IRb-60 obróbki skrawaniem zestawu detali.
PODANO W Bloggerze: Samaprawda.
PODANO W Bloggerze: Samaprawda.
To nie pracownicy POLITECHNIKI CZĘSTOCHOWSKIEJ - TO WYŻSZA KADRA -
NIEKTÓRZY Profesorowie i Władze REKTORSKIE
PODANO W Bloggerze: Samaprawda.
PODANO W Bloggerze: Samaprawda.