Centra obróbkowe przygotowane do obsługiwania przez robot przemysłowy IRb-60 obróbki skrawaniem zestawu detali
Rozdział II. Opracowanie organizacji wyposażenia gniazda obróbczego
W celu zapewnienie funkcji poszczególnych urządzeń gniazda wymienionych w poprzednim rozdziale, niezbędnym jest wyposażenie gniazda obróbczego w specjalne oprzyrządowanie i onarzędziowanie.
Jak wcześniej nadmieniono będą wykorzystane narzędzia stosowane w operacjach wykonywanych na centrach obróbczych w dotychczasowym procesie technologicznym. Przewiduje się też w określonych przypadkach (rozdz.1) wykonanie nowych narzędzi. Do obróbki otworów wierconych i gwintowanych zostaną zastosowane wielowrzecionowe głowice wiertarskie i gwinciarskie (umożliwiające jednoczesną obróbkę kilku otworów) wraz z uchwytami gwinciarskimi i wiertarskimi.
W celu zapewnienia szybkiego i sprawnego mocowania odlewów na stołach centrów obróbczych zaprojektowano dwie konstrukcje uchwytów hydraulicznych oznaczonych symbolami P1 i P2. Każda konstrukcja
zostanie wykonana w dwóch egzemplarzach oznaczonych symbolami: P1 i P1’oraz P2 i P2’. Uchwyty te zostaną umieszczone na stołach centrów obróbczych parami, tj. na OB1 – P1 i P2, a na OB2 – P1' i P2’. Pozwoli to na jednoczesną obróbkę korpusów w obydwu centrach obróbczych. W uchwycie P1 (PI’) znajduje się pięć stanowisk do mocowania odlewu odpowiadające poszczególnym rodzajom kadłubów będących przedmiotami omawianej technologii. W uchwycie P2 (P2') mamy cztery stanowiska, ponieważ kadłuby W-2,5 i WK-5 będą obrabiane w jednym stanowisku uchwytu.
Szybkie mocowanie i odmocowanie odlewów zapewniają łapy napędzane hydraulicznie.
Zaletą takiego rozwiązania uchwytów jest to, że zmiana rodzaju obrabianego detalu (z wymienionych w streszczeniu) nie pociąga za sobą konieczności wymiany uchwytów obróbkowych na stołach centrów obróbczych.
Ponadto w skład wyposażenia gniazda obróbczego wejdą dwa odkurzacze przemysłowe produkcji Gliwickiej Fabryki Urządzeń Wentylacyjnych " GLIWENT " [16].
Przedmioty do obróbki będą pobierane z palety (zagadnienia związane a ewentualną aplikacją układu identyfikujące ego położenie detalu oraz wyposażenie gniazda obrończego w urządzenia specjalne z tym związane omawia się szczegółowo w rodziałach III i TI). Przewiduje się umiejscowienie palety na stoliku, którego konstrukcja będzie umożliwiała ustawianie go nad stolikiem pozycjonującym (rys. 6).
Obrabiane detale będą składowane w magazynie wyjściowym, którym będzie pojemnik lub palety - odpowiednie rozwiązanie przyjmie się zgodnie z zaleceniem zleceniodawcy.
Manipulacje detalami w obrębie gniazda obróbczego będą wykonywane za pomocą chwytaka elektromagnetycznego sztywnego (rozdz. I i III).
Rozdział III. Projekt aplikacji urządzenia podająco-orientującego oraz adaptacji wyposażenia specjalnego stosowanego do robota IRb-60 do obróbki korpusów CGŁ.
Punktem wyjścia do analizy ewentualnej aplikacji urządzenia podająco-orientującego w zmodernizowanych procesach technologicznych jest strona ekonomiczna przedsięwzięcia.
Biorąc pod uwagę, że program rocznej produkcji wynosi dla poszczególnych detali odpowiednio:
- WR 1,5 - 1800 - 2000 szt.,
- WR 2,5 - 3400 - 3500 szt.,
- WR 5 - 2800 szt.,
- WK 1,3 - 5500 - 6000 szt.,
- PZ - 2500 szt.,
nieopłacalnym staje się stosowanie urządzenia podająco-orientującego ze względu na duży koszt oprogramowania jego aplikacji dla danego wyrobu oraz ze względu na długi czas uruchamiania każdego z programów.
W takim wypadku ekonomicznie uzasadniony rozwiązaniem jest pobieranie detali z palety. Gniazdo obróbcze wymaga operatora nadzorującego pracę gniazda. Operator ten będzie jednocześnie układał detale w palecie. W sumie cel zostanie osiągnięty bez ponoszenia dodatkowych kosztów.
Przy przyjęciu takiego rozwiązania z wyposażenia specjalnego stosowanego do robota IRb-60 do obróbki korpusów CGŁ w przedmiotowych procesach technologicznych zostanie wykorzystana konstrukcja chwytaka elektromagnetycznego sztywnego. Konstrukcja ta będzie aplikowana do wszystkich pięciu korpusów będących przedmiotem opracowywanej zmodernizowanej technologii.
W konstrukcji chwytaka elektromagnetycznego sztywnego wymianie ulegną nakładki do chwytania detalu mieszczące się na powierzchni czołowej chwytaka. Ich wielkość dostosowana będzie do największego z detali będących przedmiotami opracowywanej technologii. Chwytak elektromagnetyczny sztywny będzie stosowany we wszystkich czynnościach transportowych w obrębie gniazda obróbczego, a więc:
- pobieranie detali z palet i ustawianie ich w uchwytach obróbkowych,
- transport detali między uchwytami,
- składowanie detali w magazynie wyjściowym.
Pomijając jednak względy ekonomiczne aplikacji urządzenia identyfikacji położenia odlewu można rozpatrywać gniazdo obróbcze z punktu widzenia badawczo-doświadczalnego, pod kątem nadania mu w przyszłości struktury elastycznej.
Przyjęcie więc do dalszych rozważań omawianego stanowiska jako prototypu gniazda o strukturze elastycznej, poszczególnym układom funkcjonalnym (rozdz. VI) należy przyporządkować następujące jednostki sprzętowe:
a) układ wykonawczy - stolik pozycjonujący z napędami, magazyn wejściowy (usunięciu ulega stolik z paletami), chwytak elektromagnetyczny elastyczny (do pobierania detalu z magazynu wejściowego i przeniesienia go na stolik pozycjonujący),
b) układ zasilania - energią - napędu stolika pozycjonującego,
c) układ zbierania i wstępnego przetwarzania informacji
- w zakresie zbierania - czujnik wizyjny układu identyfikacji położenia odlewu, czujnik obciążenia chwytaka elektromagnetycznego elastycznego,
- w zakresie wstępnego przetwarzania: interfejsy czujnika wizyjnego i czujnika obciążenia chwytaka elektromagnetycznego elastycznego,
d) układ sterujący: mikrokomputer sterujący stolikiem pozycjonującym
e) układ komunikacji zewnętrznej:
- układ wyjść
- układ identyfikacji położenia, magazynu wejściowego.
Rozpoznanie położenia kolejno wprowadzanych odlewów wykonywane jest przez układ identyfikacji, złożony z czujnika wizyjnego i mikrokomputera. Rozwiązanie współpracy układu identyfikacji z układem sterowania robota należy ująć z uwzględnieniem ewolucji systemu (szczegółowo opisuje się to zagadnienie w rozdz. VII).
Jako pierwszą z tych modyfikacji proponuje się zastąpienie mikrokomputera ZX Spectrum przez procesor przystosowany do pracy w układach automatyki przemysłowej. Powinien on być przy tym modułem mikrokomputerowego systemu automatyki, co pozwoli w kolejnych etapach automatyzacji obróbki korpusów wyeliminowanie stolika pozycjonującego, a następnie wykorzystanie procesora jako jednostki centralnej układu sterowania gniazdem obróbczym. Najkorzystniejsze byłoby zastosowanie 16-bitowych modułów MM 16 ( 8086) i in. systemu INTELDIGIT-PROWAY. Istnieją także inne, równoważne funkcjonalnie, lecz 8-bitowe (ok. 4-krotnie tańsze) systemy automatyzacji mikrokomputerowej (31, 32, 36) wśród których szerokim zestawem oferowanego sprzętu i oprogramowania wyróżniają się MISTER-Z80 i MIKROSTER. Celowe będzie wybranie z wymienionych systemów tego, którego aplikacja będzie mogła być wdrożona najszybciej.
Ważnym zagadnieniem jest wybór rodzaju czujnika wizyjnego. W grę wchodzą tutaj następujące możliwości:
- kamera TV,
- kamera CCD,
- linijka świetlna CCD,
- tranzystorowa linia skanująca (na fototranzystorach).
Największą elastyczność systemu w sensie możliwości adaptacji do zmiennych warunków pracy, zapewniają kamery. Z nich większą szybkość i dokładność przetwarzania obrazu zapewnia kamera CCD. Pozyskanie takiej kamery, wg informacji uzyskanej u wyłącznego dysponenta krajowego matryc CCD (produkcji zakładów Tesla) - MERA-PIAP, jest możliwe nie wcześniej nié w roku 1989. Jej koszt będzie przypuszczalnie kilkakrotnie wyższy, niż kamery telewizyjnej. Dostawa tej ostatniej potwierdzona jest na rok 1990. W tej sytuacji do wykorzystania na aktualnym etapie pracy pozostają czujniki, co nie przekreśla zastosowania kamer 2-D w przyszłości.
Linijka świetlna CCD mogłaby być dostarczona wraz z interfejsem w I kwartale 1988 r. Zdecydowano się więc na zastosowanie tranzystorowej linii skanującej. Jej rozdzielczość wynosi 2 mm (ilość punktów odczytu – 105), co pozwala na uzyskanie identyfikacji położenia wystarczająco dokładnej dla układu pozycjonującego i robota. Określenie dokładności rozpoznawania obrazu w warunkach eksploatacyjnych przy różnym oświetleniu wymaga przeprowadzenia badań doświadczalnych w warunkach rzeczywistych.
Linijka CCD zapewnia ponad dwukrotnie większą rozdzielczość i większą powtarzalność odczytów, lecz problemem przy jej zastosowaniu może być błąd paralaksy. Jego eleminacja będzie wymagała umieszczenia linijki świetlnej w odległości rzędu paru metrów od pola obserwacji, przy zabezpieczeniu pełnej nieruchomości linijki względem tego pola.
|
REKLAMA |
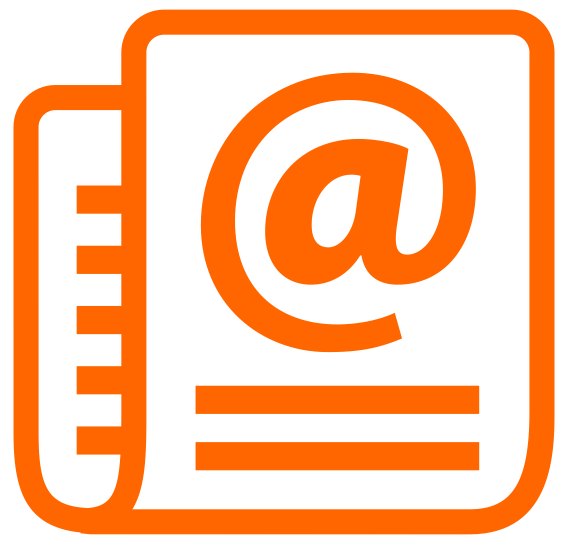
REKLAMA |
REKLAMA |
REKLAMA |
REKLAMA |
|
Studenci i absolwenci ... Grupa zrzeszająca studentów i absolwentów Politechniki Białostockiej |
![]() |
|
Oświetlenie oświetlenie in general ;-) |
![]() |
|
Elektroenergetycy Zapraszam serdecznie wszystkich, których pasją lub zamiłowaniem jest zajmowanie się wysokim napięciem, ... |
![]() |
|
Elektryka Samochodowa Grupa skierowana do osób zajmujących się profesjonalnie lub amatorsko elektyrką samochodową. |
![]() |
REKLAMA |
Gość
17:12
13 kwiecień 2012
Kto dokonał zniszczenia:Centra obróbkowe przygotowane do obsługiwania przez robot przemysłowy IRb-60 obróbki skrawaniem zestawu detali.
PODANO W Bloggerze: Samaprawda.
PODANO W Bloggerze: Samaprawda.
To nie pracownicy POLITECHNIKI CZĘSTOCHOWSKIEJ - TO WYŻSZA KADRA -
NIEKTÓRZY Profesorowie i Władze REKTORSKIE
PODANO W Bloggerze: Samaprawda.
PODANO W Bloggerze: Samaprawda.