

Polacy opracowali unikatową metodę detekcji uszkodzeń materiałów kompozytowych
Urządzenie do wibrotermograficznej detekcji uszkodzeń materiałów, w tym głównie kompozytów, opracował zespół naukowców z Akademii Górniczo-Hutniczej w Krakowie. Metoda pozwala na błyskawiczne wyszukiwania mikrouszkodzeń np. w poszyciach samolotów. Jak poinformował kierownik zespołu badawczego prof. Tadeusz Uhl, jest to pierwsza tego typu technologia opracowana w Polsce. Podobne rozwiązania wdrożyły firmy niemieckie i amerykańskie.
„Nasza metoda jest tak samo dokładna, jak inne dostępne w tym zakresie. Jej podstawowe zalety to, w porównaniu z klasyczną metodą ultradźwiękową, bardzo krótki czas pomiaru wynoszący od kilku do kilkunastu sekund oraz możliwość badania całych konstrukcji bez konieczności demontażu ich na mniejsze elementy” - zaznaczył prof. Uhl.
Dr inż. Mariusz Szwedo z zespołu badawczego wyjaśnił, że wibrotermograficzna metoda detekcji uszkodzeń bazuje na pomiarze temperatury na powierzchni badanego obiektu przez wysokiej klasy kamerę termowizyjną.
Do badanej struktury jest dostarczana energia w postaci sygnału ultradźwiękowego, który napotykając na uszkodzenie materiału powoduje zjawisko tarcia, co wytwarza ciepło. Cieplejsze strefy są lokalizowane właśnie za pomocą bardzo czułej kamery termowizyjnej.
Informacja diagnostyczna opracowywana jest przez specjalizowane oprogramowanie komputerowe na podstawie serii zmierzonych obrazów termograficznych.
Naukowcy z AGH opracowali dwa typy urządzenia: stacjonarne do użytku w warunkach laboratoryjnych i mobilne do badania dużych konstrukcji, w tym np. samolotów.
„Coraz więcej konstrukcji wykorzystuje kompozyty, czego najlepszym przykładem są nowoczesne samoloty. Trzeba je regularnie badać pod kątem wystąpienia mikrouszkodzeń, co uziemia samoloty na co najmniej kilkanaście godzin. W metodzie wibrotermograficznej pomiar trwa nieporównanie krócej” - podkreślił prof. Uhl.
Według niego, metoda ma zastosowanie w wielu gałęziach przemysłu, wszędzie tam gdzie występują materiały metaliczne i kompozytowe, a także połączenia śrubowe, nitowane, spawane i klejone.
Krakowski zespół pracuje nad technologią od dwóch lat. Obecnie powstała już wersja finalna urządzenia, która pomyślnie przeszła testy w Polskich Zakładach Lotniczych w Mielcu. W najbliższym czasie będą nim testowane łopaty turbiny gazowej na zlecenie dużej firmy z branży energetycznej. W przyszłości konstruktorzy chcą uzyskać dla metody certyfikaty światowych instytucji z branży lotniczej i energetycznej.
„Urządzenie było już prezentowane na konferencjach i targach, gdzie spotkało się z olbrzymim zainteresowaniem” - poinformował prof. Uhl. Jego rynkowa cena wyniosłaby około 500 tys. zł, podczas gdy urządzenia zagraniczne tego typu kosztują w granicach 1 mln zł.
Projekt badawczy współfinansowany jest ze środków unijnych w ramach Programu Operacyjnego Innowacyjna Gospodarka.
REKLAMA |
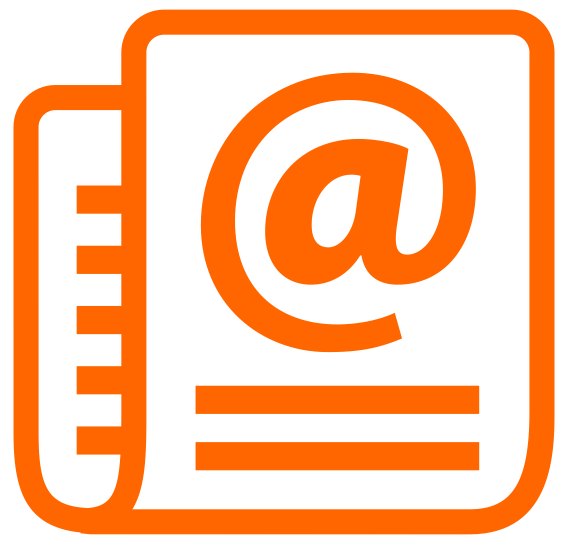
REKLAMA |
REKLAMA |