

Zwiększenie wydajności obrabiarek CNC przez stosowanie w obróbce gładkościowo-dokładnościowej nagniatania wielokulkowymi toczno-ślizgowymi narzędziami
2.9. Patent nr 90376 - Urządzenie do dogniatania zewnętrznych powierzchni kulistych, zwłaszcza powierzchni uszczelniająco - zamykających zawieradeł do kulowych zaworów kurkowych; (foto 10.)
Twórcy wynalazku: Bogdan Zając (Politechnika Częstochowska), Henryk Żegunia, Stanisław J. Szeląg; opublikowano 30.07.1977 r.
Przedmiotem wynalazku jest urządzenie do nagniatania zewnętrznych powierzchni kulistych.
Urządzenie to ma tuleję lub podobny element względnie układ elementów, wewnątrz którego znajduje się co najmniej jeden rowek, mający korzystnie postać płaskiej, zamkniętej linii kołowej, w którym są umieszczone elementy nagniatające (robocze), korzystnie w kształcie kulek, tworzące w rowku obieg zamknięty i zabezpieczone przed wypadaniem z niego przez zmniejszenie jego szerokości od wewnętrznej strony tulei.
W wyniku zastosowania urządzenia według wynalazku uzyskano znaczne obniżenie pracochłonności i innych kosztów w procesach wytwarzania zawieradeł do zaworów kulowych, a jednocześnie ~ bardzo w tym przypadku istotny i pożądany -- wzrost gładkości, twardości oraz odporności na ścieranie, korozję i erozję zewnętrznych, kulistych powierzchni uszczelniająco-zamykających tych zawieradeł, co z kolei zwiększa ich trwałość i przedłuża żywotność. Uzyskuje się ponadto poprawę w zakresie wzajemnej zamienności detali, to jest zawieradeł oraz elementów z nimi współpracujących i współdziałających, a zwłaszcza siedlisk uszczelniających w kadłubach zaworów, co dodatkowo upraszcza procesy wytwarzania, montażu i remontowo-naprawcze, a także gospodarkę magazynową i podobną.
Z uwagi na masową produkcję różnorakich typów i odmian zaworów kulowych, a nadto z uwagi na dalsze, szerokie możliwości zastosowania wynalazku w procesach wytwarzania bądź napraw różnych innych detali, poza zawieradłami do tych zaworów--wynalazek przynosi wyraźne efekty techniczne oraz ekonomiczne i jest przydatny dla gospodarki i przemysłu.
Wynalazek został zilustrowany w przykładach wykonania i zastosowania na rysunku, na którym fig. 1 przedstawia przekrój pionowy kulistego zawieradła oraz urządzenia nagniatającego, przy czym zawieradło jest osadzone na trzpieniu mocująco-napędzającym, fig. 2'-- szczegół według fig. 1 w powiększeniu, a fig. 3 -- w ujęciu schematycznym, dalszy przykład dogniatania powierzchni kulistej.
Proces dogniatania powierzchni kulistych 1, 1a (fig. 1-3), przy zastosowaniu urządzenia według wynalazku, można najwygodniej przeprowadzić na frezarce, zarówno pionowej jak i poziomej, przy czym w przypadku nagniatania według fig. 3 (powierzchnia 1a), konieczne jest zastosowanie frezarki ze skrętnym stołem albo skrętną głowicą (frezarka uniwersalna).
Przed rozpoczęciem procesu nagniatania, powierzchnia 1, 1a zostaje odpowiednio wstępnie przygotowana, na drodze obróbki skrawaniem lub/oraz przy zastosowaniu innych procesów, w zakresie właściwej dokładności wymiarowej, kształtowej i gładkościowej, jak również np. pod względem twardości, struktury tworzywa, odporności na korozję oraz innych, podobnych cech.
Kuliste zawieradło 2 (fig. 1' i 2) osadza się nieruchomo, za pośrednictwem znajdującego się w nim współśrodkowego, kołowo-walcowego otworu przepływowego, na trzpieniu 3, a następnie całość mocuje się w kłach napędzanej podzielnicy oraz konika frezarki.
W głowicy narzędziowej frezarki zamocowane zostaje urządzenie nagniatające; oś obrotu 4 tego urządzenia przecina się z osią obrotu 5 kulistego zawieradła 2 i trzpienia 3, pod kątem prostym, w geometrycznym środku zawieradła 2, czyli w środku powierzchni nagniatanej 1.
Fig. 3 ukazuje schematycznie przykład dogniatania powierzchni 1a kulistego czopa. W tym przypadku osie obrotu 4a oraz 5a przecinają się, w środku kulistej powierzchni 1a pod kątem różnym od prostego. W skrajnym przypadku układ mocowania przedmiotu nagniatanego może się tu różnić od poprzednio opisanego, ze względu na niemożność podparcia tegoż przedmiotu, po stronie prawej, w koniku.
W związku z tym można zastosować mocowanie jednostronne, np. w podzielnicy z uchwytem samocentrującym.
Główną częścią składową urządzenia dogniatającego według wynalazku (fig. 1 i 2) jest element podobny w swym kształcie do zbieżnej tulei 6, przechodzącej po stronie mniejszej średnicy we współśrodkowy z nią czop 7, służący do połączenia urządzenia z elementami napędowymi np. z głowicą narzędziową frezarki. Po przeciwnej, otwartej stronie jest do czołowej powierzchni tulei 6 przymocowany, wkrętami 8, pierścień 9 o przekroju poprzecznym podobnym do litery ,Z" Między czołowa powierzchnią tulei 6 a ramionami pierścienia 9 jest w wyniku tego utworzony pierścieniowy rowek, wypełniony - najlepiej wzdłuż całego swego obwodu -- elementami dogniatającymi (roboczymi) 10, mającymi korzystnie kształt kulek.
Aby przeprowadzić proces nagniatania powierzchni kulistej 1 bądź 1 a, powierzchnię tę wprawia się w ruch obrotowy odpowiednio wokół osi 5 lub 5a, a jednocześnie nadaje się ruch obrotowy urządzeniu nagniatającemu, odpowiednio wokół osi 4 albo 4a. Równocześnie -- rzecz jasna -- dociska się urządzenie do przedmiotu nagniatanego (bądź odwrotnie--przedmiot do urządzenia) z odpowiednią siłą, w kierunku osi obrotu 4 względnie 4a urządzenia. Elementy nagniatające (kulki) 10, tocząc się po nagniatanej powierzchni 1, 1a, poruszają się zarazem we wzmiankowanym wyżej, pierścieniowym rowku, stanowiącym ich prowadnicę, tworząc obieg zamknięty.
Ewentualna zmiana kierunku ruchu obrotowego nagniatanego przedmiotu oraz/albo urządzenia nagniatającego może w niektórych przypadkach pozytywnie wpływać na jakość uzyskiwanej powierzchni. Z tej samej przyczyny prędkość obrotowa przedmiotu i urządzenia powinny się między sobą różnić. Chodzi mianowicie o to, aby tor ( linia styku)danej kulki dogniatającej, opisywany przez nią na powierzchni nagniatanej, nie nakładał się na siebie.
2.10. Patent nr 100671 - Urządzenie do nagniatania wewnętrznych powierzchni kulistych
Twórcy wynalazku: Bogdan Zając Politechnika Częstochowska, Henryk Żegunia, Stanisław J. Szeląg; opublikowano 15.02.1979 r.
Przedmiotem wynalazku jest urządzenie do nagniatania wewnętrznych powierzchni kulistych, które może znaleźć zastosowanie w procesach wytwarzania oraz regeneracyjnych i naprawczych różnych elementów, zwłaszcza metalowych.
Dotychczas nie były znane urządzenia specjalnie przystosowane i przeznaczone do nagniatania wewnętrznych powierzchni kulistych. Znane i stosowane są jedynie rozwiązania zbliżone do przedmiotu wynalazku, jak np. urządzenie według opisu patentowego PRL nr 68265, przeznaczone do nagniatania otworów kołowo-walcowych, mające budowę następującą:
Wewnątrz korpusu, mającego kształt tulei, osadzony jest suwliwie trzpień, wystający obustronnie poza korpus. Jeden koniec trzpienia ma kształt znanego stożka Morse'a i służy do osadzania urządzenia w gnieździe konika tokarki. Na drugim końcu trzpienia znajduje się układ nagniatający, składający się ze stożkowego pierścienia nałożonego na trzpień i opierającego się o kołnierz tegoż trzpienia, pierścienia oporowego przylegającego do czoła korpusu, kulek nagniatających umieszczonych pomiędzy wymienionymi wyżej pierścieniami: stożkowym i oporowym, oraz koszyczka zabezpieczającego kulki przed wypadaniem. Omawiane urządzenie wyposażone jest ponadto w układ ustalania położenia korpusu względem trzpienia, a tym samym - ustalania promieniowego rozstawu kulek nagniatających. Promieniowy przesuw kulek powodowany jest przez wspomnianywyżej pierścień stożkowy, pod wpływem siły pochodzącej do sprężyny umieszczonej wewnątrz korpusu. Średnica promieniowego rozstawienia kulek jest oczywiście zmniejszana w celu swobodnego wprowadzania urządzenia do cylindrycznego otworu nagniatanego, a następnie wysuwania z tegoż otworu, to znaczy przed rozpoczęciem i po zakończeniu właściwego procesu nagniatania.
Opisane wyżej urządzenie jest stosunkowo skomplikowane i złożone w swej budowie, a w konsekwencji -- -pracochłonne w wykonaniu i drogie. Urządzenie to, będąc--jak już wyżej wspomniano--przeznaczone do nagniatania otworów cylindrycznych, musi posiadać układ pozwalający zmieniać promieniowy rozstaw elementów roboczych, czyli kulek nagniatających; stąd między innymi dość złożona budowa tegoż urządzenia.
Celem niniejszego wynalazku było opracowanie w miarę możliwości prostego urządzenia do wydajnego, wygodnego i taniego nagniatania wewnętrznych powierzchni kulistych, które by zarazem gwarantowało uzyskiwanie powierzchni jednorodnej, to jest powierzchni o odpowiedniej równomierności zgniotu, a w konsekwencji o równomiernie podwyższonej twardości, wysokiej gładkości, a jednocześnie dużej odporności na ścieranie i erozję, z równoczesnym podwyższeniem odporności na korozję. Cel ten osiągnięto w wyniku konstrukcyjnego opracowania urządzenia, które zawiera co najmniej dwa elementy nagniatające w kształcie brył obrotowych -- przykładowo w kształcie kulek -- rozmieszczone w jednakowej odległości od punktu, który w czasie prowadzenia procesu nagniatania pokrywa się z geometrycznym środkiem nagniatanej powierzchni kulistej. Wspomniane elementy nagniatające są przy tym korzystnie umieszczone w rowku bądź rowkach, na obwodzie tarczy urządzenia lub/oraz na obwodzie podobnego albo dodatkowego, czyli dalszego jego eiementu, względnie układu elementów -przy czym tenże rowek bądź rowki mają korzystnie postać płaskich linii kołowych. Elementy nagniatające wypełniają najlepiej rowek całkowicie, to jest wzdłuż całego jego obwodu, tworząc w nim obieg zamknięty, przy czym jednocześnie elementy te są zabezpieczone przed wypadaniem z rowka w ten sposób, że jego szerokość od strony zewnętrznej (otwartej) jest zmniejszona.
W wyniku wynalazku pojawiła się możliwość wydajnego i niedrogiego uzyskiwania wewnętrznych powierzchni kulistych o wysokiej jakości, a w szczególności o dużej gładkości, a zarazem znacznej odporności na ścieranie, korozję i erozję, przy czym należy dodać, że uzyskiwane powierzchnie są bardzo jednorodne co do swych, wymienionych wyżej, pożądanych a korzystnych cech i własności. Tym samym wynalazek spełnia podstawowe wymogi, to znaczy wnosi do stanu techniki zarówno nowe wartości (efekty) techniczne, jak i ekonomiczne. Wynalazek znajdzie zastosowanie przede wszystkim w przemyśle budowy maszyn i innych urządzeń, przy wytwarzaniu, ewentualnie naprawach, różnych detali, w szczególności metalowych.
Przedmiot wynalazku jest przedstawiony w przykładzie wykonania na rysunku, na którym fig. 1 przedstawia urządzenie do nagniatania, częściowo w widoku, a częściowo w osiowym przekroju wzdłużnym, a fig. 2 -- schemat nagniatania wewnętrznej powierzchni kulistej przy zastosowaniu tegoż urządzenia.
Element podstawowy urządzenia (fig. 1) stanowi płaska, okrągła tarcza 1 z trzpieniem 2, który służy do połączenia urządzenia ze źródłem napędu, np, z głowicą narzędziową frezarki. Pomiędzy powierzchnią obwodową tarczy 1 oraz dwoma przytwierdzonymi do niej rozłącznie, jednakowymi nakładkami 3, utworzony jest pierścieniowy rowek, wypełniony wzdłuż całego obwodu rzędem elementów nagniatających 4, mających kształt kulek. Wymiary i ukształtowanie rowka są tak dobrać, że elementy 4, czyli kulki, mogą się w nim swobodnie obracać we wszystkich kierunkach, a tym samym – tworząc obieg zamknięty - mogą się w nim także toczyć po obwodzie tarczy l, przy czym jednocześnie są one zabezpieczone przed wypadaniem z rowka przez jego zwężenie od strony otwartej, czyli zewnętrznej. Urządzenie, a zwłaszcza kulki oraz ich bieżnia, czyli powierzchnia obwodowa tarczy 1, jak również odpowiednie powierzchnie nakładek 3, powinny być wykonane przy zachowaniu odpowiednich warunków w zakresie dokładności wymiarowej i kształtowej, gładkości, twardości oraz rodzaju tworzywa (korzystnie stal w stosowanym gatunku, przy zastosowaniu właściwej obróbki cieplnej). Jako pewną analogię można tu wskazać łożyska toczne.
Figura 2 ilustruje, w ujęciu schematycznym, proces nagniatania wewnętrznej powierzchni kulistej 5, przy zastosowaniu opisanego wyżej urządzenia według fig. 1. Płytkę 6, zawierającą nagniataną powierzchnię 5. wprawia się w ruch obrotowy wokół osi centralnej 7, przechodzącej przez geometryczny środek tej powierzchni 5.
Jednocześnie wprawia się w ruch obrotowy urządzenie nagniatające, przy czym osią obrotu jest oś 8, nachylona pod pewnym kątem do osi 7 i przecinająca się z nią we wspomnianym powyżej, geometrycznym środku nagniatania powierzchni 5. Zarazem urządzenie dociska się do powierzchni 5 (lub odwrotnie - płytkę 6 do urządzenia) zakreśloną siłą, w kierunku osi 8. Jak przy tym widać z rysunku (fig. 2!, kąt zawarty pomiędzy osiami 7 i 8, usytuowanie powierzchni 5 na sferze kulistej 9 i wymiary tej powierzchni 5' oraz wymiary urządzenia, a zwłaszcza jego średnicę zewnętrzną, czyli średnicę d koła opisanego na elementach nagniatających 4--wiążą w zasadzie pewne, określone zależności geometryczno-wymiarowe. Nie jest jednakże przy tym w zasadzie wykluczone, przeprowadzenie procesu nagniatania powierzchni5 przy użyciu urządzenia o średnicy d większej od średnicy minimalnej, wynikającej z rysunku (fig. 2). Rzecz jasna, w taki", przypadku kąt zawarty pomiędzy osiami 7 oraz 8 będzie wtedy inny, a konkretnie --zwiększy się w stosunku dc sytuacji przedstawionej rysunkiem (fig. 2), a poza tym --pewna część obwodu urządzenia, czyli pewna ilość elementów nagniatających 4 (coraz to innych), będzie się stale znajdować poza nagniataną powierzchnia 5.
W trakcie procesu nagniatania, elementy (kulki) 4 toczą się po powierzchni - 5, a jednocześnie przemieszczają się w swojej prowadnicy, czyli w rowku urządzenia, na zasadzie obiegu zamkniętego.
Jeżeli chodzi o kierunki ruchu obrotowego nagniatanej powierzchni 5 (czyli płytki 6) oraz urządzenia, odpowiednio wokół osi 7 oraz 8, to kierunki te są w zasadzie dowolne. Korzystnym jednakże oczywiście na ogół jest, dla uzyskania większej prędkości ruchu względnego, a tym samym nagniatania oraz skrócenia czasu trwania operacji, gdy ruchy te pomijając, rzecz jasna, w tych rozważaniach sprawę kąta nachylenia między osiami 7 oraz 8 - odbywają się w kierunkach przeciwnych, to znaczy np. tak, jak zaznaczono strzałkami na rysunku fig. 2). Z zagadnieniem tym wiąże się ponadto sprawa doboru właściwych prędkości obrotowych (kątowych) oraz ich wzajemnego stosunku. W każdym przypadku obydwie te prędkości powinny się między sobą różnic, najkorzystniejsza zaś sytuacja ma miejsce wtedy, gdy stosunek jednej prędkości do drugiej jest liczbą niewymierna. Chodzi bowiem o to, aby tor danego elementu nagniatającego 4, nie nakładał się cyklicznie sam na siebie, po wykonaniu Drze2 urządzenie oraz płytkę 6 pewnej liczby obrotów. Sprawa ta może mieć istotne znaczenie z punktu widzenia efektów procesu nagniatania, czyli jakości uzyskanej finalnie powierzchni 5. Podobnie, w niektórych przypadkach, pozytywny wpływ na jakość może mieć także zmiana (zmiany) kierunku ruchu obrotowego urządzenia lub (oraz płytki 6) w trakcie wykonywania procesu na jednym wyrobie, to jest na danej płytce 6.
Obowiązują ponadto oczywiście ogólne, powszechnie znane zasady i parametry przeprowadzania procesów nagniatania, np. w zakresie odpowiedniego przestrzegania wysokiej czystości (bardzo ważne) -- itp.
Nagniatanie wewnętrznej powierzchni kulistej według wynalazku można przeprowadzić najlepiej na frezarce uniwersalnej bądź na innej podobnej obrabiarce przy czym - rzecz jasna - urządzenie to musi reprezentować odpowiednio wysoką klasę sprawności wyposażenia, dokładności i precyzji.
|
REKLAMA |
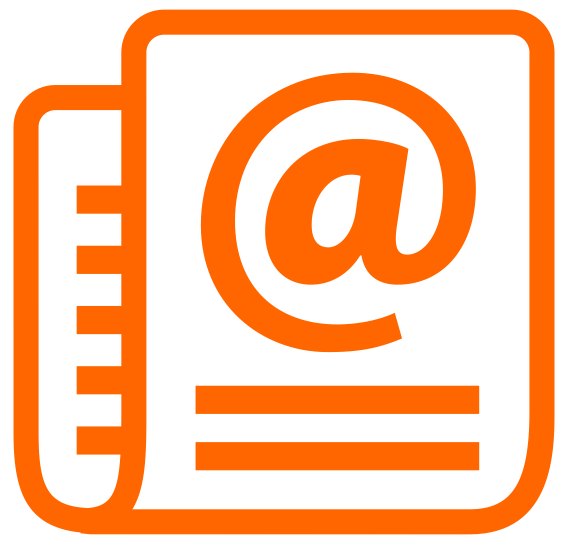

REKLAMA |
REKLAMA |
REKLAMA |
REKLAMA |
|
POMOC elektroonline.pl Masz problem z jakąś funkcjonalnością portalu, nie możesz dodać zdjecia video?? pisz pomożemy!! |
![]() |
|
PHP PHP: problemy,porady,ciekawe rozwiązania |
![]() |
|
KOŁA SEP Studenckie, pracownicze czy inne - wszystkie koła związane z działalnością Stowarzyszenia ... |
![]() |
|
Oświetlenie samochodowe Grupę dedykuję problemom i pomysłom związanym z realizacją oświetlenia samochodowego, światła do ... |
![]() |
REKLAMA |