

Przejrzystość danych - klucz do zoptymalizowanego działania SmartWire-DT integruje podzespoły maszyn z komunikacją
Aby zmniejszyć koszty związane z cyklem życia maszyny, potrzebne są szczegółowe dane na temat jak największej liczby jej podzespołów. Dzięki systemowi inteligentnego okablowania wdrożonemu na poziomie urządzenia nawet najprostsze podzespoły automatyki bez możliwości autonomicznej komunikacji mogą w wydajny pod względem kosztów sposób zostać przekształcone w inteligentne urządzenia dostarczające wartościowych danych na potrzeby optymalizacji produktywności, sprawniejszego monitorowania stanu tych urządzeń oraz diagnostyki predyktywnej.
Nieprzerwanie rosnąca presja związana z kosztami, coraz silniejszą konkurencją, internacjonalizacją i globalizacją ma duży wpływ na etap projektowania. Wyzwania te stawiają na czele koszty operacyjne, głównie z racji faktu, iż maszyn zasadniczo używa się przez dziesięciolecia, a nie tylko przez kilka lat. W rezultacie koszty operacyjne szybko przekraczają koszty zakupu – w perspektywie dziesięcioletniego okresu często okazuje się, że koszty eksploatacyjne już pięcio- lub dziesięciokrotnie przewyższają koszty inwestycji.
Wymagane są szczegółowe informacje
Przejrzystość danych jest kluczowa do utrzymania kosztów w ryzach w trakcie cyklu życia maszyny oraz do rozpoznawania okazji do zmniejszania tych kosztów – przestojów można uniknąć jedynie przez stosowanie diagnostyki predyktywnej i serwisowania w sytuacji, w której znane są szczegółowe dane dotyczące tak wielu podzespołów maszyny, jak to tylko możliwe do zarejestrowania. Co więcej, posiadanie tych informacji gwarantuje możliwość używania maszyny na najwyższych obrotach bez ryzyka przestoju. Aby podejmować rozsądne decyzje i dokonywać trafnych prognoz dotyczących stanu maszyny, potrzebny jest szeroki zakres danych, takich jak informacje o stanie, temperaturach, czasie przełączania i zużyciu energii maszyn.
Zasadniczo większość nowoczesnego i skomplikowanego sprzętu posiada własną elektronikę, która umożliwia rejestrowanie danych, a czasem nawet ich wstępne przetwarzanie. Niemniej jednak sytuacja staje się zupełnie inna, gdy mamy do czynienia z dużą liczbą podzespołów wcześniej podłączonych okablowaniem sterowniczym do cyfrowych lub analogowych wyjść i wejść używanych systemów zarządzania. W takim przypadku inteligentne okablowanie i system komunikacji, taki jak SmartWire-DT firmy Eaton, oferuje proste, szybkie i opłacalne rozwiązanie zapewniające osiągnięcie pożądanego poziomu przejrzystości danych. Taki system nie wymaga tradycyjnego połączenia punkt-punkt z systemem zarządzania w celu okablowania indywidualnych przełączników, czujników i urządzeń napędowych – zamiast tego wszystkie urządzenia są połączone przy pomocy 8-żyłowej, zielonej taśmy z prostym złączem wtykowym. Oprzewodowanie SmartWire-DT zasila podłączone urządzenia, jednocześnie zapewniając wymianę danych.
Moduły komunikacyjne jako ulepszenie prostych urządzeń
Poza prostą i szybką instalacją niewątpliwą zaletą takiego systemu są jego specjalne moduły komunikacyjne. Są to przede wszystkim elektroniczne układy scalone typu ASIC wyposażone w interfejsy pozwalające na odbiór cyfrowych i analogowych sygnałów pomiarowych oraz procesor pozwalający na wykonywanie niezależnych algorytmów Tych wydajnych i kompaktowych modułów można więc używać wraz z prostymi urządzeniami elektrycznymi, takimi jak rozruszniki silnikowe czy wyłączniki, które rejestrują i wstępnie przetwarzają informacje, w prosty sposób wcielając te elementy w proces gromadzenia danych. Wcześniej wymagało to instalacji odpowiednich styków pomocniczych i wejść cyfrowych, a także odpowiednio rozbudowanej infrastruktury, co wymuszało bardziej zaawansowane planowanie i opracowywanie bardziej skomplikowanych projektów maszyn.
Nawet rozbudowane maszyny można szybko łączyć
Moduły komunikacyjne SmartWire-DT pozwalają na bezpośrednią integrację podłączonych urządzeń z centralnym systemem zarządzania lub z istniejącym już środowiskiem komunikacyjnym danej maszyny. Dotyczy to zarówno przycisków, styczników, prostych przełączników, czujników, jak i jednostek generujących znaczne ilości cyfrowych i analogowych danych procesowych, na przykład wyłączników silnikowych wyposażonych w elektronikę pomiarową, urządzeń łagodnego rozruchu oraz przemienników częstotliwości. Można podłączyć aż 99 urządzeń do taśmy o maksymalnej długości do 600 metrów. Moduły IP67 I/O umożliwiają szybkie podłączenie nawet najbardziej rozbudowanych maszyn z setkami czujników. Jeżeli w późniejszym czasie konieczna będzie rozbudowa, wystarczy podłączyć nowy moduł do przewodu komunikacyjnego i zamontować nowy czujnik. Użytkownik może podłączyć nowe urządzenia do magistrali przesyłowej za pomocą złącza wtykowego i skonfigurować je poprzez wciśnięcie przycisku –proces niemal tak prosty jak w systemach Plug and Play. Zastosowanie kosztownych elementów magistrali obiektowej o wysokim stopniu ochrony nie jest już prawie w ogóle potrzebne, a stosowane wcześniej okablowanie pośrednie można w znacznym stopniu ograniczyć lub w ogóle z niego zrezygnować.
Wartość dodana w całym cyklu życia
Korzystanie z tej technologii zapewnia bezpośrednią wartość dodaną przez cały cykl życia maszyny. Na etapie projektowania można lepiej i łatwiej planować jednostki logiczne, co pozwala zmniejszyć nakłady na projektowanie nawet o 70%, zaś nakłady na okablowanie, testowanie i rozruch można obniżyć nawet o 85%. W ogólnym rozrachunku system oparty na inteligentnym okablowaniu może obniżyć koszty wynikające z cyklu życia instalacji elektrycznej aż o 30%, zaczynając od projektu, a kończąc na serwisowaniu i konserwacji. Niemniej jednak do najważniejszych zalet wynikających z osiągnięcia przejrzystości danych należą usprawnienie diagnostyki i konserwacji oraz zwiększone wykorzystanie możliwości maszyny.
Dzięki temu przykładowo wyłącznik silnikowy zintegrowany z maszyną przy pomocy SmartWire-DT może rejestrować istotne dane, takie jak natężenie prądu silnika, przeciążenia i użyteczne dane diagnostyczne, przed przesłaniem tych informacji do aplikacji w celu dalszego przetwarzania. Użytkownik może więc w porę wykrywać krytyczne obciążenia silnika oraz, w razie zbliżającego się wyłączenia, podjąć z wyprzedzeniem konieczne kroki w celu uniknięcia wyzwolenia wyłączników zabezpieczających silnik i związanej z tym awarii napędu. Rejestrowanie natężenia prądu silnika pozwala również na ciągłą pracę napędów ze zwiększoną wydajnością, co przekłada się na zwiększone możliwości maszyny bez ryzyka powstania przestoju spowodowanego przeciążeniem. Jeśli jednak doszłoby do awarii, wyłącznik silnikowy dostarczy szczegółowych informacji o jej przyczynie, np. o zaniku fazy.
Inteligentny układ okablowania i system komunikacji na poziomie urządzeń pozwala producentom maszyn i integratorom systemów z łatwością rejestrować wszystkie wymagane przez operatora dane w celu wyświetlenia ich w układzie sterowania lub wyświetlenia wewnętrznych wskaźników.
Podstawa dla koncepcji czwartej rewolucji przemysłowej
Możliwe jest również połączenie z systemem chmury, ponieważ SmartWire-DT można przy pomocy modułów gateway podłączyć do wszystkich standardowych w przemyśle magistrali obiektowych – czyli do Internetu Rzeczy (Internet of Things, IoT). Umożliwia to wykorzystanie danych w czasie rzeczywistym przy użyciu usług w chmurze, takich jak monitorowanie stanu. Nawet jeżeli producent maszyn w przyszłości zmieni swoje podejście do zarządzania, to urządzenia peryferyjnego lub systemu okablowania nie trzeba ponownie projektować, ponieważ zazwyczaj wystarczy wymienić gateway. Oznacza to, że nowe standardy w komunikacji, takie jak OPC UA, są już obsługiwane. Integratorzy systemów mają również dostęp do danych dotyczących maszyny i jej podzespołów przez Internet i mogą używać ich na przykład do diagnostyki i konserwacji.
Co więcej, moduły komunikacyjne SmartWire-DT nie tylko zapewniają wysoką przejrzystość danych, ale też zmieniają każde urządzenie w urządzenie inteligentne, które mogą pracować niezależnie od siebie w sposób rozproszony, co jest podstawowym elementem idei Industry 4.0.
Więcej szczegółowych informacji dotyczących przejrzystości danych przy użyciu SmartWire-DT można znaleźć w raporcie „Inteligentne okablowanie zapewnia przejrzystość konstruowania instalacji przemysłowych”. Jest on dostępny do pobrania bezpłatnie na stronie www.eaton.eu/pl/iw/sys.
Autor: Heribert Einwag, Product Manager, Eaton
REKLAMA |
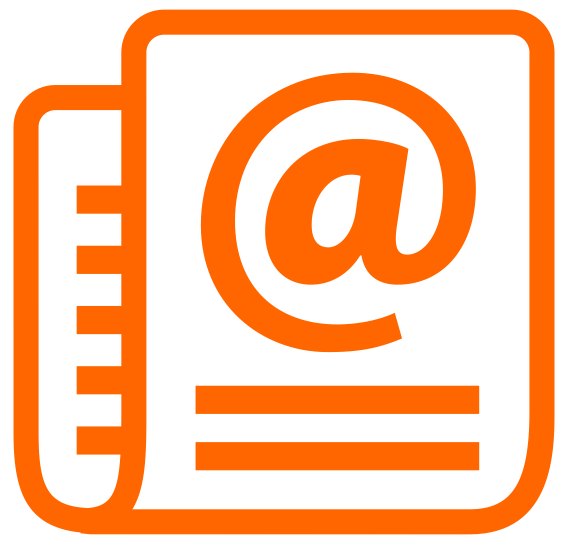
REKLAMA |
REKLAMA |