

Polska inżynieria powierzchni dotarła na powierzchnię komety
Dziś miało miejsce pierwsze w historii ludzkości lądowanie na powierzchni komety. Na odległej od Ziemi o 475 milionów kilometrów komecie 67P/Czuriumow-Gierasimienko osiadł lądownik Philae europejskiej misji Rosetta w celu przeprowadzenia badań geologicznych na jej powierzchni. W podłoże wbije się penetrator MUPUS, skonstruowany specjalnie do prac w mikrograwitacji. Wyjątkowe parametry mechaniczne elementów penetratora, gwarantujące jego działanie w ekstremalnych warunkach panujących na komecie, osiągnięto dzięki metodzie inżynierii powierzchni opracowanej na Wydziale Inżynierii Materiałowej Politechniki Warszawskiej.
Na powierzchni komety 67P/Czuriumow-Gierasimienko osiadł lądownik Philae europejskiej misji Rosetta. Uwieńczona sukcesem operacja oznacza, że już wkrótce zostaną podjęte pierwsze w dziejach prace geologiczne na powierzchni komety. W jej podłoże wbije się penetrator MUPUS, zbudowany w Centrum Badań Kosmicznych Polskiej Akademii Nauk w Warszawie. Aby zagwarantować niezawodne działanie urządzenia w warunkach środowiska komety, elementy konstrukcyjne MUPUS-a poddano jednej z nowatorskich metod obróbek powierzchniowych, opracowanych na Wydziale Inżynierii Materiałowej Politechniki Warszawskiej (WIM PW).
Penetrator geologiczny MUPUS to elektromagnetyczne urządzenie skonstruowane w taki sposób, aby podczas wbijania trzpienia w powierzchnię komety nie przenosić sił na lądownik. Liczne elementy penetratora wykonano ze stopu tytanu – materiału lekkiego, lecz o stosunkowo niskiej twardości. Aby powierzchnie elementów osiągnęły parametry mechaniczne wymagane dla urządzenia dedykowanego do prac geologicznych, należało je zmodyfikować za pomocą odpowiedniego procesu obróbki powierzchniowej. Warszawscy inżynierowie zaproponowali węgloazotowanie jarzeniowe.
– Trzeba pamiętać, że sam lot sondy do komety zajął 10 lat. Gdy pracowaliśmy nad elementami kosmicznego młotka, węgloazotowanie jarzeniowe stopów tytanu było technologią nowatorską w skali światowej – podkreśla prof. dr hab. inż. Tadeusz Wierzchoń (WIM PW). Węgloazotowanie tytanowych elementów MUPUS-a, polegające na wprowadzaniu atomów azotu i węgla w ich warstwy wierzchnie, zostało przeprowadzone w niskotemperaturowej plazmie poprzez połączenie procesów azotowania i nawęglania jarzeniowego. W jego wyniku powierzchnia obrabianych detali stała się twarda, odporna na ścieranie, a jej współczynnik tarcia, szczególnie istotny dla elementów mechanicznych współpracujących w próżni, był niski. Jednocześnie tak wytworzona dyfuzyjna warstwa powierzchniowa węgloazotka tytanu charakteryzowała się dobrą przyczepnością do podłoża.
Jakość elementów penetratora MUPUS, poddanych obróbce na Wydziale Inżynierii Materiałowej PW, oceniały niezależne, renomowane instytucje naukowe, m.in. Space Research Institute (Institut für Weltraumforschung, IWF) w Graz w Austrii oraz Max Planck Institute for Aeronomy w Lindau w Niemczech (obecnie Max Planck Institute for Solar System Research).
Dziś inżynierowie WIM PW stosują i rozwijają różne procesy obróbek jarzeniowych tytanu i jego stopów (w tym na potencjale plazmy), umożliwiające wytwarzanie m.in. złożonych warstw kompozytowych. Używane obecnie procesy pozwalają zachować pełną kontrolę nad strukturą, składem fazowym i chemicznym oraz gładkością powierzchni wytwarzanych warstw, umożliwiają więc precyzyjne kształtowanie właściwości obrabianych wyrobów w zależności od ich przeznaczenia. Jednocześnie metody te gwarantują wytwarzanie dyfuzyjnych warstw o jednorodnej grubości na detalach o bardzo skomplikowanych kształtach.
– Świetnym przykładem możliwości obróbek jarzeniowych tytanu i jego stopów są elementy pompy wirowej wspomagającej pracę serca, nad którymi obecnie pracujemy. Zawierają one m.in. detale o grubości zaledwie 0,4 mm, z otworami średnicy 0,6 mm. Innymi słowy, mamy do dyspozycji metody inżynierii powierzchni, które można stosować nawet w przypadku obróbki powierzchniowej tych wyrobów, gdzie wymagana tolerancja wymiarowa sięga mikrometrów – mówi prof. Wierzchoń.
Doskonałe własności mechaniczne i biologiczne elementów poddanych obróbce powierzchniowej na Wydziale Inżynierii Materiałowej PW znalazły zastosowanie w najbardziej zaawansowanych technologicznie projektach. Oprócz narażonych na bezpośredni kontakt z krwią elementów pompy wirowej wspomagającej pracę serca i elementów zastawek serca, warszawscy inżynierowie przygotowują m.in. elementy protezy stawu biodrowego, stenty, implanty kostne stymulujące wzrost tkanki kostnej, a także części silników lotniczych i narzędzia o zwiększonej trwałości i niezawodności, wykonane z węglików spiekanych.
REKLAMA |
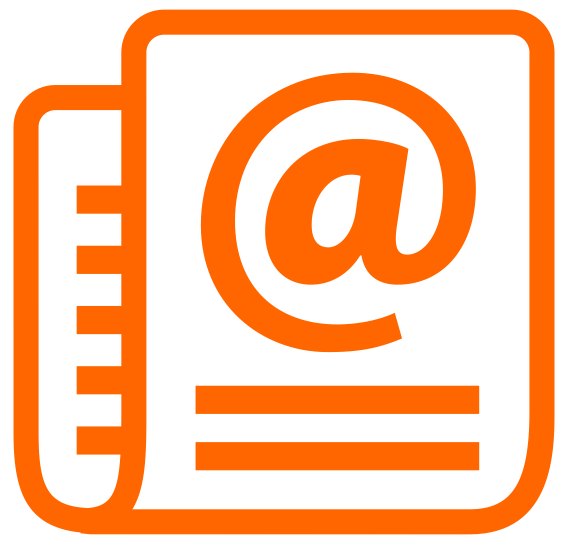
REKLAMA |
REKLAMA |