

Materiały o podwyższonej przewodności cieplnej dla obrabiarek i procesorów
Materiały nowej generacji, które znacznie lepiej przewodzą ciepło, umożliwią dalszą miniaturyzację sprzętu elektronicznego, usprawnią działanie tarcz hamulcowych i obrabiarek
Stworzenie nowych materiałów, które będą miały wyższa przewodność cieplną – to cel projektu TERMET. Na ten czteroletni projekt przeznaczono blisko 24 mln złotych dofinansowania z Programu Operacyjnego Innowacyjna Gospodarka. Jakie możliwości otworzyły przed uczonymi te pieniądze i jakie branże mogą odnieść korzyści z zastosowania wyników ich badań – mówi dr. inż. Łukasz Ciupiński z Uczelnianego Centrum Badawczego „Materiały Funkcjonalne” Politechniki Warszawskiej.
Jak wyjaśnia kierownik projektu, przewodnictwo cieplne jest istotne dla przemysłu elektronicznego oraz dla producentów rozmaitych elementów, do których wytworzenia używane są urządzenia skrawające lub obrabiarki. Ta również oferta dla przemysłu motoryzacyjnego, przede wszystkim firm produkujących motocykle. Wyzwania związane z miniaturyzacją i rosnącą wydajnością sprzętu komputerowego powodują, że urządzenia nagrzewają się coraz bardziej. Również podczas pracy obrabiarek i hamulców powstaje niepożądane ciepło, które obniża sprawność układów, zwiększa ryzyko awarii i strat produkcyjnych. Odprowadzenie energii cieplnej na zewnątrz urządzenia umożliwiają m.in. materiały o bardzo dużym przewodnictwie cieplnym. Nad technologiami tworzenia kompozytów, które spełniają taką funkcję, pracuje zespół uczonych projektu TERMET.
- Kompozyty tworzy się łącząc laboratoryjnie materiały, które w naturze nie mogłyby utworzyć połączenia chemicznego. Na przykład diamentu z miedzią, który to kompozyt mógłby posłużyć do chłodzenia urządzeń elektronicznych, np. procesorów w komputerach. Połączenie dobrze przewodzącego metalu z wysoko przewodzącym materiałem ceramicznym, jakim jest diament to nie jest nasz oryginalny pomysł. W literaturze od ponad 10 lat można spotkać publikacje na ten temat. Cały projekt opiera się wszakże na opanowaniu technologii wytwarzania tych materiałów. Są one na tyle skomplikowane, że powszechnie się tych materiałów nie stosuje – tłumaczy dr inż. Ciupiński.
Jak wyjaśnia badacz, miedź nie łączy się z diamentem, dlatego technologia wymaga wiele badań i odpowiedniej modyfikacji składników nowego materiału.
- To juz nam się udało w skali laboratoryjnej. Jednak przejście od próbki do wyprodukowania demonstracyjnej podkładki pod procesor wymaga dalszej pracy. Z pewnością pomoże w tym nowe urządzenie zakupione w ramach projektu, które pozwala na osiągnięcie wyższej temperatury syntezy naszych kompozytów. Nasza technologia opiera się na spiekaniu proszków z wykorzystaniem prądu elektrycznego, dlatego potrzebowaliśmy baterie kondensatorów, które będą w stanie wygenerować solidny impuls elektryczny. Urządzenie zostało zmodernizowane, dzięki czemu będą powstawać coraz większe próbki – zapowiada Ciupiński.
Pieniądze z programu Innowacyjna Gospodarka umożliwiły zakup trzech głównych urządzeń. Największe z nich, mikrotomograf rentgenowski pozwala na nieinwazyjne obserwowanie wewnętrznej struktury nowego materiału, sprawdzenie jakości komponentów, ich rozmieszczenie w przestrzeni. Sprzęt wart ponad 2,5 mln zostanie na uczelni, a ponieważ ma szersze zastosowania, z pewnością po zakończeniu projektu posłuży do wielu badań. Kolejny nabytek to urządzenie za ok 1 mln zł instalowane w Instytucie Techniki Cieplnej. Pozwala ono na pomiar dyfuzyjności cieplnej czyli właściwości, na podstawie której można obliczyć współczynnik przewodności cieplnej. Trzeci to piec za około 650 tys. zł, którego potrzebowali uczeni z Akademii Górniczo-Hutniczej do wytwarzania ceramiki. Część środków to materiały potrzebne do eksperymentów. Dodatkowe fundusze pozwoliły na sfinansowanie prac zespołu, który liczy około 35 osób.
W składzie współrealizatorów projektu nie ma firm komercyjnych. Współrealizuje go Akademia Górniczo-Hutnicza w Krakowie i trzy jednostki na Politechnice Warszawskiej: Uczelniane Centrum Badawcze Materiały Funkcjonalne – główny beneficjent, Wydział Inżynierii Materiałowej i Instytut Techniki Cieplnej na wydziale Mechanicznym Energetyki i Lotnictwa.
- To jest projekt badawczy, choć o charakterze aplikacyjnym. Próbujemy nawiązać współpracę z firmami, które potencjalnie będą zainteresowane wdrożeniem opracowanych przez nas materiałów do swoich rozwiązań i produktów. Były kontakty z kilku firm polskich, mamy też roboczy kontakt z firmą globalną. Myślimy o współpracy z firmami, które wytwarzają narzędzia skrawające czy obrabiarki, bo w tym obszarze jesteśmy w stanie zaoferować atrakcyjny produkt – deklaruje dr inż. Ciupiński. W jego ocenie, stosowanie nowych materiałów będzie się opłacało producentom urządzeń elektronicznych.
- Stać nas na to, żeby włożyć taki element do laptopa. Telefony komórkowe to również prawdopodobne zastosowanie dla naszych materiałów, bo trudno wyobrazić sobie wentylator w takim telefonie. Aby odprowadzić ciepło na zewnątrz potrzebne są materiały o wysokim przewodnictwie cieplnym. I to będzie się opłacało, bo rynek domaga się produktów coraz mniejszych, telefonów wyposażonych w funkcje, jakich kilka lat temu nie miały nawet komputery – uważa badacz.
Jego zdaniem jest to również atrakcyjna oferta dla firm wykorzystujących w swojej produkcji obrabiarki. Również te urządzenia nagrzewając się wolniej pracowałyby efektywniej. W obrabiarkach są wprawdzie stosowane systemy chłodzenia cieczami chłodzącymi, ale jeśli samo narzędzie będzie mogło szybciej oddać ciepło do cieczy chłodzącej, to sprawniejszy będzie ów mechanizm chłodzenia.
- O tym, że nowe technologie są potrzebne, świadczy presja rynku, jaką odczuwamy na własnej skórze. Otrzymaliśmy zapytania od firmy prowadzącej obróbkę cieplną detali. Przy zastosowaniu miedzi do odprowadzania ciepła pojawia się tam poważny problem - część elementów pęka. Szybkość odprowadzania ciepła jest zbyt mała i pojawia się zbyt duża różnica temperatur prowadząca do zmian wymiarowych obrabianych detali. Usprawnienie procesu może uratować część produkcji tej firmy – opowiada dr inż. Ciupiński.
Jak podkreśla, właśnie tu zaczyna się rachunek ekonomiczny – czy robimy po staremu i mamy większą ilość wybrakowanych produktów, które trzeba wyrzucić lub przerobić na nowe, czy stosujemy nową technologię. „Jeśli przetestujemy nowy materiał i ilość braków będzie znacząco mniejsza, to nawet poważna zmiana sprzętu może się opłacać” – ocenia kierownik projektu TERMET.
Uczeni pracują nad kompozytem aluminium i węglika krzemu. Taki materiał będzie lekki, co wiąże się z małą bezwładnością, a to przy szybkoobrotowych obrabiarkach może wpłynąć na poprawę precyzji ruchu narzędzia tnącego.
- Każdy element, który znajduje się w ruchu, gdzie kierunek i prędkość zmieniają się dość często, co jest cechą obrabiarek precyzyjnych, podlega zjawisku bezwładności. Znamy to zjawisko z życia codziennego. Kiedy obiekt o dużej masie, na przykład samochód, wchodzi w zakręt z dużą prędkością, wówczas prawdopodobnie wypadnie z zakrętu. To właśnie to zjawisko. Kiedy zmniejszymy masę, czyli na przykład wejdziemy w ten sam zakręt motocyklem przy tej samej prędkości – jest większa szansa, że manewr się powiedzie. Zmniejszając masę elementów, jakie muszą poruszać się w obrabiarkach, możemy sprawić, by urządzenia były bardziej precyzyjne i być może szybsze, a więc efektywniejsze – uzasadnia dr inż. Ciupiński.
Nowe materiały mogą ponadto ulepszyć działanie tarcz hamulcowych w szybkich motocyklach. W czasie procesu hamowania wytwarzane jest bowiem dużo ciepła. Im bardziej hamulce się rozgrzewają, pracują dłużej, tym gorzej działają. Dlatego ważne jest, żeby odprowadzić ciepło z układu hamulcowego. Jednocześnie ważna jest kwestia współczynnika tarcia. Materiał jaki będzie zastosowany na tarczę hamulcową w zestawieniu z parą „tarcza – klocek” musza mieć wysoki współczynnik tarcia, żeby proces hamowania przebiegał efektywnie.
- W naszym projekcie nastawiamy się na współpracę z przemysłem motocyklowym, ponieważ tam stosowane są systemy pracujące krótko i bardzo intensywnie. Ze względu na prędkości jakie rozwijają zaawansowane motocykle, układy hamulcowe są bardziej wymagające. Drugie zastosowanie to układy hamulcowe do samolotów, które potrzebują zmaksymalizować efekt hamowania w momencie lądowania – wylicza uczony.
Obszary zastosowania nowo wytworzonych materiałów przewiduje się w nowoczesnych gałęziach gospodarki jak elektronika czy fotonika, a także w energetyce, mechanice precyzyjnej i transporcie.
REKLAMA |
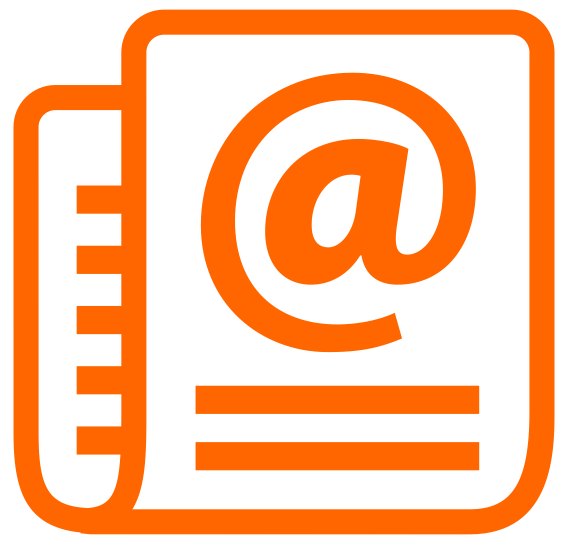
REKLAMA |
REKLAMA |