

General Electric pracuje nad trójwymiarowym drukowaniem części
General Electric (GE) wraz z European Aeronautic Defence and Space Company (EADS, ang. Europejski Koncern Lotniczo-Rakietowy i Obronny) pracują nad trójwymiarowym drukowaniem i zastosowaniem tej technologii do wytwarzania części lotniczych i aparatury medycznej. Drukowane części są wytrzymałe, lżejsze i tańsze niż odlewane lub skrawane – poinformował magazyn Technology Review.
GE uruchomiło specjalne laboratorium w Niskayuna, stan Nowy Jork, które ma opracować własną technologię trójwymiarowego wydruku. Koncern liczy że poza dotychczas wdrażanymi zastosowaniami w branży lotniczej i medycznej, nowymi technikami wytwarzania komponentów zainteresuje się też branża motoryzacyjna i budowy maszyn
Technika wydruku trójwymiarowego komponentów jest znana od dwóch dziesiątek lat, ale jej zastosowanie było dotąd bardzo ograniczone. Używano jej do wytwarzania dedykowanych podzespołów w produktach małoseryjnych, prototypach i do modyfikacji znanych już rozwiązań. Była ona bowiem droga i ograniczała się do obróbki kilku podstawowych materiałów jak stopy specjalne, brązy, mosiądze oraz plastiki.
Obecnie trójwymiarowy wydruk może być stosowany do wszystkich typów stopów stalowych i metali kolorowych oraz spieków ceramicznych, stopów aluminium i tytanu. Wzrosła także dokładność obróbki – dziś wynosi ona dziesiąte części mikrometra.
Inżynierowie z nowego laboratorium w Niskayuna, prowadzą obecnie prace nad stworzeniem nowego typu sprzętu medycznego, głównie ultrasonografów, których GE jest jednym z największych producentów.
Elementem newralgicznym ultrasonografu jest głowica, w której sygnały elektryczne przetwarzane są na ultradźwięki. Głowica składa się z tysięcy małych kolumn, o długości 30-40 mikrometrów. GE do tej pory korzystało ze specjalnego laserowego noża wycinającego je bardzo wolno z przygotowanej bardzo cienkiej płytki ceramicznego spieku. Obecnie chce je drukować, co przyspieszy cały proces, zmniejszy jego koszty i ułatwi zachowywanie wymiarów.
Drukowanie jest wykonywane z proszku stopu ceramicznego czułego na ultrafiolet na podkładce polimerowej. Dysze drukarki nadają wydrukowanej warstwie odpowiedni kształt, a stop jest utwardzany przy pomocy ultrafioletu. Po utwardzeniu zostaje naniesiona następna warstwa stopu, która także będzie utwardzana ultrafioletem i dalej aż do wydrukowania całych kolumn.
Jak powiedział Technology Review, Prabhjot Singh inżynier mechanik z GE Research, ze względu na nowatorską koncepcje wydruku, technologia wymaga jeszcze dopracowania. Badacze z GE mają nadzieje, ze pozwoli ona nie tylko na obniżkę kosztów ultrasonografów, ale także na zwiększenie ich rozdzielczości.
GE zaczyna w podobny wytwarzać części do silników lotniczych i mechaniki skrzydła samolotów. Chodzi zwłaszcza o odlewane dotąd i obrabiane skrawaniem elementy klap skrzydłowych. Drukowanie ich na tytanowym rdzeniu, z podgrzanej laserami warstwy proszku metalicznego, zwiększa wytrzymałość nowej części, i zmniejsza jej wagę przy znacznej redukcji kosztów.
W laboratorium badawczym euro koncernu zbrojeniowego i aerokosmicznego EADS, w Filton, w Wlk. Brytanii, z kolei prowadzi się próby nad zastosowaniem techniki wydruku trójwymiarowego wytwarzaniu kluczowych elementów silników lotniczych. Stosuje się przy tym technikę zwaną additive layer manufacturing (ALM).
W ALM lasery dużej mocy tworzą z proszku metalicznego o drobnych ziarnach, włókien węglowych lub wzmacnianych tworzyw sztucznych cienką warstwę metalu lub kompozytu. Na tą warstwę nakładane są następne aż do osiągnięcia zakładanego kształtu i grubości zaprojektowanej wcześniej części. EADS wytwarza tą techniką drobniejsze części turbin silników turboodrzutowych i podobnie jak GE – elementy mechaniki skrzydła. Są one o około 50 proc. lżejsze niż wykonywane w tradycyjny sposób.
Według EADS redukcja masy samolotu pasażerskiego ,a zwłaszcza silnika, choćby o jeden kilogram przynosi zysk na paliwie rzędu 100 tys. USD w czasie 30 lat – zakładanym całkowitym okresie eksploatacji maszyny pasażerskiej.
REKLAMA |
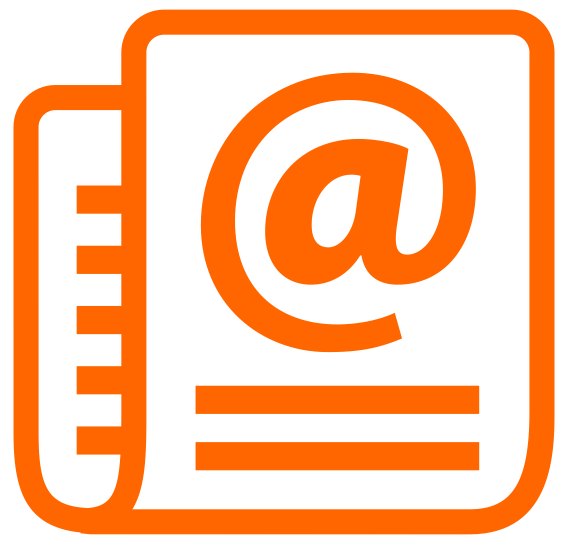
REKLAMA |
REKLAMA |