

Elektryka w podczerwieni
Kamery termowizyjne stały się już niemal podstawowym narzędziem w diagnostyce maszyn i urządzeń elektroenergetycznych. Tych, którzy podchodzą jeszcze sceptycznie do termowizji, spróbujemy przekonać do tej technologii.
To może zacznijmy zatem od początku, czyli od historii termowizji, nazywanej także termografią. Mówi się, że jej geneza sięga początku XIX w. Wiąże się ona z badaniami nad rozpraszaniem światła za pomocą pryzmatu. Angielski astronom William Herschel, prowadzący badania, zaobserwował interesujące zjawisko podczas rzutowania na kartkę papieru barwnej wiązki światła słonecznego, które rozszczepione jest przez pryzmat. Powierzchnia kartki ulega bardziej intensywnemu ogrzaniu po stronie czerwonej barwy, a także poza nią. Autor eksperymentu doszedł do wniosku, że zbiorniczki termometrów, umieszczone na powierzchni papieru, są w stanie rejestrować różne wartości temperatury w strefie poszczególnych barw oraz poza nimi. Tak właśnie odkryto zjawisko promieniowania cieplnego w zakresie podczerwieni. W połowie XX w. zaczęto stosować zjawisko promieniowania podczerwonego, najpierw w wojsku, a potem w użytku cywilnym.
Można zatem powiedzieć, że termowizja stanowi proces obrazowania w paśmie średniej podczerwieni, w efekcie czego możliwe jest rejestrowanie promieniowania cieplnego, emitowanego przez ciało fizyczne w zakresie temperatur spotykanych w warunkach codziennych bez dodatkowego oświetlenia. Termowizja stanowi więc rodzaj aparatu fotograficznego, który pracuje w podczerwieni. Każde ciało, które osiąga temperaturę wyższą od temperatury zera bezwzględnego, emituje fale nazywane promieniowaniem podczerwonym lub cieplnym. Intensywność promieniowania jest wprost proporcjonalna do czwartej potęgi temperatury badanego obiektu. Stąd też dokonując pomiaru promieniowania cieplnego określonego obiektu, mierzymy jego temperaturę. Przyjmuje się jednak, że model ten nie jest idealny a badane obiekty odbiegają od niego. Kluczowe miejsce zajmuje zatem uwzględniany w pomiarach współczynnik emisyjności, dobierany dla konkretnego materiału. Stanowi on miarę danego ciała do emisji promieniowania cieplnego. W efekcie badania termowizyjnego powstaje termogram, który stanowi przedstawienie promieniowania z jednoczesnym uwzględnieniem rozkładu temperatur badanej powierzchni.
Fot. 1. Termogramy
Termowizja w elektroenergetyce
Fot. 2. Kamera Flir i60. Urządzenie cechuje się niewielką masą i rozdzielczością 180 x180 pikseli. Przewidziano także wbudowany aparat cyfrowy. W urządzeniu uwzględniono funkcję Obraz w Obrazie (PiP), łączącą obraz widzialny z termowizyjnym dla profesjonalnych analiz. Wskaźnik laserowy z markerem na termowizyjnym obrazie wyświetlanym na ekranie LCD sprawia, że inspekcje elektryczne i mechaniczne są bardziej wydajne. |
Fot. 3. Kamera Flir T365. Możliwe jest nagrywanie notatek głosowych – do poszczególnych zdjęć z możliwością wprowadzania ich do raportu. Opcjonalnie dostępne obiektywy 6º, 15º, 45º, 90º, 2x i 4x, łatwe w montażu do korpusu kamery, dzięki czemu zyskuje się dużą różnorodność zastosowań urządzenia. Standardowa karta pamięci SD umożliwia zapis ponad 1000 zdjęć pomiarowych w formacie JPEG. |
Fot. 4. Kamera termowizyjna Testo 882 o ergonomicznym kształcie pistoletu, z rozdzielczością 320 × 240 pikseli. W urządzeniu przewidziano standardowy obiektyw 32°. Możliwe jest wyświetlanie wilgotności powierzchni. Jakość obrazu NETD < 60 mK. |
Co dokładnie można diagnozować za pomocą kamery termowizyjnej? Na termogramie poszczególnym barwom, przyporządkowana jest temperatura odpowiadająca skali. W praktyce w kolorach jasnych, oznacza się powierzchnie o wyższej temperaturze, zaś barwami ciemniejszymi przedstawia się niższe temperatury. Obróbka danych odbywa się przy użyciu specjalistycznego oprogramowania komputerowego. W zależności od temperatury badanego obiektu, podejmowane się późniejsze działania. W ramach nich rozróżnia się tzw. zalecenia miękkie oraz zalecenia ostre. Zalecenia miękkie występują w przypadku, gdy przyrost temperatury badanego obiektu wynosi:
- ponad 50K - konieczna jest natychmiastowe podjęcie działań,
- 30K do 50K - niezbędna jest naprawa tak szybko jak to tylko możliwe,
- 10K do 29K - należy podjąć działania w pierwszym możliwym terminie,
- mniej niż 10K - należy monitorować obiekt.
Zwróćmy uwagę, że zalecenia miękkie determinowane są przez wiele czynników. Przede wszystkim chodzi o możliwość wystąpienia większych obciążeń prądowych oraz skutków ewentualnej awarii. W badaniach termowizyjnych często uwzględnia się nadwyżkę temperatury, która określana jest jako różnica pomiędzy temperaturą wadliwego obiektu a temperaturą takich samych elementów, które pracują w dwóch pozostałych fazach. Badania powinny być przeprowadzone przy pełnym obciążeniu prądowym. Zalecenia ostre występują wtedy, gdy przyrost temperatury badanego obiektu wynosi:
- ponad 30K - należy podjąć działania natychmiastowo,
- do 30K - należy podjąć działania jak najszybciej,
- do 5K - należy monitorować obiekt.
Kamery termowizyjne są dobrym narzędziem przy diagnostyce rozdzielni elektrycznych. W tym obszarze spektrum zastosowań kamer jest bardzo szerokie. Obejmuje ono bowiem szyny zbiorcze, odłączniki a także wyłączniki mocy oraz przekładniki i transformatory. Podczas pomiarów, w pierwszej kolejności, przeprowadzane jest badanie mające charakter bardziej ogólny, po którym odbywa się szczegółowa analiza. Na termografie zostają zaznaczone miejsca o podwyższonej temperaturze, na co składa się wiele przyczyn. Mogą to być chociażby niewłaściwie obrobione końcówki przewodów czy też wadliwe podłączenia do zacisków. Za pomocą termowizji sprawdzić możemy również transformatory. Kontrolowana jest wtedy zewnętrzna powierzchnia kadzi z olejem a także osprzęt, izolatory przepustowe oraz elementy przyłączeniowe. Jedną z kluczowych kwestii stanowi kontrola termowizyjna pokrywy transformatora. Termowizja bardzo dobrze sprawdza się przy wykrywaniu asymetrii zasilania lub przeciążeń w instalacjach. Termogramy są niezastąpione przy diagnozowaniu silników elektrycznych. Kamer termowizyjnych użyć możemy do sprawdzania poprawności działania złącz elektrycznych, które nie powinny wykazywać podwyższonej temperatury, względem łączonych elementów. Pamiętać jednak należy, że w czasie długiej eksploatacji instalacji z prądem o dużym natężeniu, zmęczeniem materiału czy też korozją styków, ulega pogorszeniu stan złączy. Stąd też pole do popisu dla termowizji, dzięki której można stwierdzić wzrost temperatury złącza prądowego w stosunku do innych podzespołów pracujących w sieci.
|
REKLAMA |
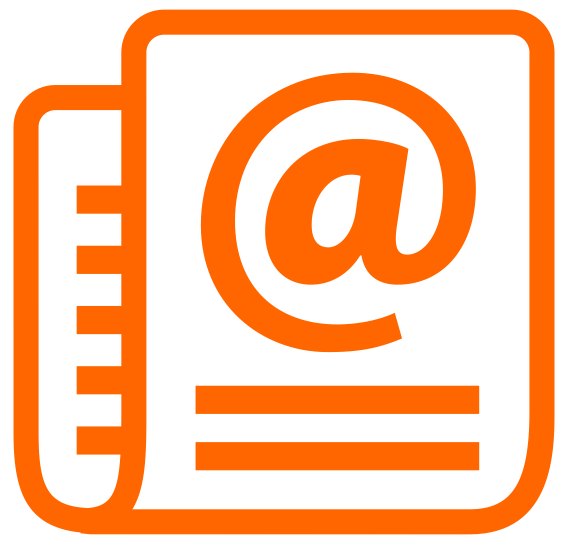
REKLAMA |