

System sterowania procesem nanoszenia wielowarstwowych powłok metalicznych metodą jonowego rozpylania
Związki międzymetaliczne oraz ich połączenia np. z węglem, azotem, krzemem czy borem stanowią grupę materiałów o różnorodnych możliwościach zastosowania, wynikających z ich specyficznych właściwości. Niektóre z nich charakteryzują się własnościami nadprzewodzącymi, inne posiadają wysoka temperaturę topnienia i dobre właściwości mechaniczne w wysokich temperaturach, jeszcze inne doskonałą odporność korozyjną, czy efekt pamięci kształtu. Związki międzymetaliczne stanowią nową generację materiałów przeznaczonych do pracy w niekorzystnych warunkach. Można je otrzymywać różnymi technikami. Jedną z najbardziej perspektywicznych jest wykorzystanie samorozwijającej się, wysokotemperaturowej syntezy SHS (ang. Self–Propagation High-Temperature Synthesis).
SHS realizowana jest w układzie zbliżonym do adiabatycznego, w którym przebiega reakcja egzotermiczna. Przebieg procesu ma charakter spalania zachodzącego w fazie stałej lub z udziałem fazy ciekłej, bądź rzadziej – gazowej. Inicjację reakcji (zapłon) uzyskuje się przez lokalne (miejscowe) lub całkowite (globalne) ogrzanie reagentów. Złożem reakcyjnym jest z reguły mieszanina mikroproszków. W odpowiednich warunkach, po inicjacji reakcji egzotermicznej powstaję fala termiczna rozprzestrzeniająca się z szybkością do 20 cm/sek., a szybkość przyrostu temperatury dochodzi do 1500oC/sek. Ze względu na te specyficzne warunki badania dotyczące kinetyki jak i mechanizmu tej reakcji, prowadzącej do powstania określonego związku międzymetalicznego, napotykają na liczne trudności. Wydaje się, że powłoka złożona z określonej sekwencji warstw stanowi układ bardzo zbliżony do złoża proszkowego, natomiast daje znacznie większe możliwości obserwacji i pomiarów pozwalających na lepsze poznanie tego procesu. Zainteresowanie procesem SHS sięga ubiegłego tysiąclecia, w którym ukazały się pierwsze prace tej tematyki [1, 2]. Wykorzystywanie wielowarstwowych powłok metalicznych do badania reakcji tworzenia się związku międzymetalicznego znajduje odzwierciedlenie w coraz liczniejszych opracowaniach [3–6].
Mając na uwadze fakt, że warunki otrzymywania powłok wielowarstwowych przeznaczonych do badań mechanizmu reakcji syntezy, muszą być precyzyjnie określone i powtarzalne, zrozumiałym jest potrzeba realizacji w miarę pełnej automatyzacji przygotowanego w tym celu stanowiska. Grubość poszczególnych powłok musi być dokładnie określona, a więc istotnym jest prawidłowe wyznaczenie szybkości nanoszenia danego materiału.
W planowanych pracach przewiduje się wykorzystanie trzech rodzajów metali: tytanu, glinu i niklu, co pozwoli na uzyskanie powłok wielowarstwowych takich jak Ti/Al, Ni/Al oraz Ti/Ni. Szybkości rozpylania tych metali są różne. Aby uzyskać pożądaną szybkość nanoszenia warstwy, niezbędne jest utrzymywanie stabilnej pracy zasilacza magnetronu oraz stabilizacja ciśnienia argonu w komorze. Istotnym jest taki dobór warunków nanoszenia, aby grubość strefy rozdziału poszczególnych warstw (tzw. intermixed region) była jak najmniejsza. Strefa rozdziału warstw utrudnia transport ciepła w strefie reakcji [3] i zmniejsza jej szybkość [5]. Analogiczne efekty zaobserwować można przy rozcieńczaniu złoża proszkowego produktem reakcji [1, 2]. Badania reakcji tworzenia związku międzymetalicznego wymagają przygotowania powłok o określonej grubości warstw i zadanej sekwencji.
Opis stanowiska technologicznego
Do budowy stanowiska wykorzystano komorę próżniową o pojemności około 50 dcm3 z układem pompującym SP-2000 składającym się z dyfuzyjnej pompy olejowej oraz pompy obrotowej.
Zawór klapowy nad pompą dyfuzyjną wyposażono w ogranicznik otwarcia, umożliwiający regulację szybkości odpompowywania komory. W komorze zainstalowano dwie wyrzutnie magnetronowe WMK50. Układ pozwala na uzyskanie ciśnienia końcowego rzędu 10-3 Pa. Ciśnienie kontrolowane jest przy użyciu próżniomierzy Inficon PSG550. Komora reakcyjna posiada płaszcz wodny z doprowadzeniem wody gorącej (stosowanej w procesie odpompowywania układu) oraz zimnej – używanej podczas nanoszenia warstw [7]. Podłoża do nanoszenia warstw umieszczano na specjalnym obrotowym stoliku. Gaz roboczy (argon) wprowadzany jest przy wykorzystaniu dwóch zaworów membranowych. Termopara umieszczona w komorze umożliwia kontrolę temperatury w trakcie procesu nanoszenia warstw. Trzy wzierniki umieszczone w ściankach komory pozwalają na bezpośrednią obserwację procesu. Ogólny widok stanowiska przedstawiono na poniższym zdjęciu:
System sterowania
W celu wytworzenia powtarzalnych struktur wielowarstwowych o zdefiniowanych i powtarzalnych grubościach, opracowano układ sterowania pracujący pod nadzorem oprogramowania napisanego w środowisku graficznym LabVIEW [8,9].
System sterujący jest systemem modułowym. Każde urządzenie wykonawcze sterowane jest bezpośrednio za pomocą dedykowanego modułu mikrokontrolera jednoukładowego. Wszystkie moduły sterujące kontrolowane są za pomocą głównego oprogramowania sterującego. Podstawowym elementem systemu jest oprogramowanie, zainstalowane na komputerze PC. Za jego pomocą realizowane jest ustawianie parametrów oraz kontrola przebiegu procesu napylania. Komunikacja pomiędzy głównym komputerem sterującym oraz modułami realizowana jest w sposób bezprzewodowy, z wykorzystaniem modułów transmisyjnych pracujących zgodnie z protokołem ZigBee [9-11]. Zwiększa to elastyczność systemu. Podłączenie nowego elementu wykonawczego do systemu związane jest jedynie z wyposażeniem go w układ komunikacji bezprzewodowej oraz zaimplementowanie w systemie centralnym odpowiedniego modułu oprogramowania.
Głowna aplikacja sterująca przesyła zadane parametry procesu do elementów wykonawczych. Po ich zaakceptowaniu i uruchomieniu procesu napylania, niemożliwa jest zmiana parametrów pracy, aż do momentu zakończenia danego cyklu napylania.
Podczas napylania moduły kontrolne dokonują odczytu informacji nt. temperatury i ciśnienia gazu roboczego i cyklicznie wysyłają ją do komputera centralnego. Dane archiwizowane są w postaci pliku dokumentującego proces technologiczny napylania wielowarstwy.
Struktura systemu sterowania
Do komputera klasy PC podłączony jest główny moduł sieci ZigBee – koordynator systemu. Sterowany jest bezpośrednio z poziomu aplikacji centralnej, za pomocą interfejsu USB. Każdy z elementów sterujących posiada własny odbiornik ZigBee z unikatowym adresem, dzięki czemu komunikacja pomiędzy systemem centralnym a modułem wykonawczym odbywa się w trybie punkt-punkt i jest niezależna od stanu pozostałej części systemu. Możliwe są również transmisje rozgłoszeniowe (broadcastowe), które w opracowanym systemie wykorzystywane są do uzyskania synchronizacji czasowej poszczególnych modułów [11]. Strukturę systemu komunikacji przedstawia rys. 1.
Rys. 1. Struktura systemu sterowania.
Po uruchomieniu głównej aplikacji inicjowane jest oprogramowanie sterujące pracę modułu koordynatora ZigBee. Oprogramowanie zarządzające układem ZigBee odpowiedzialne jest przede wszystkim za inicjalizację układu, stworzenie nowej sieci oraz wysyłanie i odbieranie wiadomości od urządzeń sterujących.
Komputer komunikuje się z układem ZigBee za pomocą zestawu komend AT, poprzez interfejs USB. Wiadomości odbierane przez oprogramowanie od modułu można podzielić na trzy kategorie:
- Informacje o statusie wykonanej operacji – w tym przypadku układ ZigBee odpowiada jednym z dwóch kodów informujących o tym, czy udało się wykonać żądaną operację.
- Dane odebrane z sieci – w tym przypadku układ ZigBee przesyła najpierw kod informujący o odebraniu danych, następnie adres urządzenia od którego pochodzi wiadomość, długość pola danych oraz dane.
- Informacja o zdarzeniu – w tym przypadku układ ZigBee przesyła specjalny kod informujący o wystąpieniu jakiegoś zdarzenia a następnie jego identyfikator. Zdarzeniem może być na przykład odłączenie od sieci któregoś urządzenia sterującego. Informacja ta może zostać wykorzystana jako swoisty alarm bezpieczeństwa, po którym oprogramowanie zakończy proces napylania (napylanie jest przeprowadzane tylko w prawidłowo funkcjonującym systemie).
Algorytm przedstawiający zasadę działania procesu sterowania przedstawiono na rysunku 2.
Rys. 2. Algorytm działania aplikacji sterującej.
Program sterujący pracą każdego z urządzeń wykonawczych (końcowych) podzielony został na dwa moduły funkcjonalne, z których jeden odpowiedzialny jest za proces sterowania urządzeniem lub czujnikiem, a drugi za obsługę modułu ZigBee. Zadania, realizowane przez moduł obsługi transmisji ZigBee, nie różnią się od zadań modułu zaimplementowanego w urządzeniu pełniącym rolę koordynatora sieci. Różnica występuje jedynie w metodzie inicjalizacji urządzenia. Komendy przesyłane do modułu ZigBee bezpośrednio po włączeniu przez użytkownika zasilania, konfigurują układ do pracy w trybie urządzenia końcowego i dołączają go do sieci zainicjowanej przez układ koordynatora (moduł koordynatora musi zostać uruchomiony jako pierwszy, wynika to z faktu, iż urządzenie końcowe można jedynie dołączyć do istniejącej sieci, którą wcześniej stworzyć musi koordynator).
|
REKLAMA |
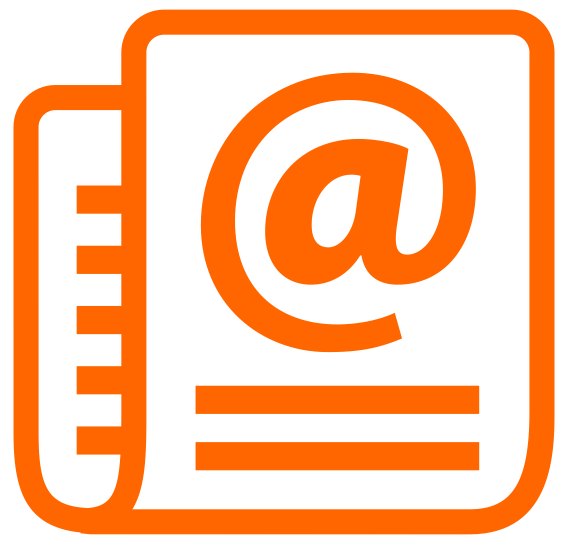
REKLAMA |