

Zastosowanie magnetyków amorficznych przy budowie transformatorów
Obserwowany w ostatnim czasie duży nacisk na ochronę środowiska naturalnego oraz obniżenie kosztów dostaw energii powoduje rozwój nowych materiałów wykorzystywanych do budowy transformatorów. Obniżenie strat wnoszonych przez te urządzenia ogranicza bowiem straty środowiskowe związane z emisją szkodliwych substancji powstałych przy spalaniu węgla lub innego medium energetycznego. Szczególnie intensywny rozwój dotyczy transformatorów dystrybucyjnych, z uwagi na ich dużą liczbę. W Polsce jest ich ponad 200 tysięcy, co stanowi 98% wszystkich zainstalowanych transformatorów.
Magnetyki amorficzne
Materiał amorficzny o nazwie metglas, mający właściwości magnetyczne i nadający się do budowy rdzeni transformatorowych, wynaleziono w latach 50. ubiegłego stulecia. Jednak zasadniczy przełom w opanowaniu technologii tych materiałów nastąpił dopiero w latach 70. w Stanach Zjednoczonych, gdzie opracowano metodę wytwarzania magnetyków amorficznych w cyklu ciągłym.
Sposób ciągłego wytwarzania metglasu (szkła metalicznego) polega na skierowaniu stabilnej strugi ciekłego metalu (najczęściej wykorzystywane jest żelazo, ale stosuje się również kobalt) na zewnętrzną powierzchnię szybko obracającego się walca (kilka tysięcy obrotów na minutę) wykonanego z metalu o dobrym przewodnictwie cieplnym. Walec ten służy do szybkiego schładzania ciekłego stopu, w wyniku czego powstaje materiał magnetyczny o właściwościach amorficznych (ciało stałe o nieuporządkowanej strukturze cząsteczkowej).
Szybkość schładzania jest rzędu 106 K/s, gdyż zbyt wolne schładzanie powoduje częściowe skrystalizowanie materiału i utratę struktury amorficznej. W ten sposób uzyskuje się taśmę amorficzną o szerokości do 12 cm i grubości od 18 do 30 μm.
W tabeli I przedstawiono parametry blachy transformatorowej amorficznej firmy Metglas Alloys. Rezystywność blach przedstawionych w tabeli I wynosi 130·10-8 Ω·m. Dla porównania rezystywność blach krzemowych zimnowalcowanych wynosi 45÷48·10-8 Ω·m.
TABELA I. Parametry blachy amorficznej firmy Metglas Alloys o grubości 30 μm
B [T] | 0,1 | 0,2 | 0,4 | 0,6 | 0,8 | 1,0 | 1,2 | 1,4 | 1,6 | |
Stratność p [W/kg] | 60 Hz | 0,0035 | 0,010 | 0,026 | 0,045 | 0,070 | 0,10 | 0,14 | 0,22 | 0,28 |
50 Hz | 0,0028 | 0,008 | 0,021 | 0,036 | 0,056 | 0,08 | 0,11 | 0,17 | 0,22 | |
Magnesowalność H [A/m] | prąd stały | 0,84 | 1,00 | 1,10 | 1,18 | 1,26 | 1,35 | 1,6 | 5,6 | 8,0 |
Rdzenie transformatorowe wykonane z metglasu
Jedną z metod konstrukcji rdzeni amorficznych jest zwijanie taśmy amorficznej w walce o średnicach równych średnicy jarzma i kolumny. Uzyskane w taki sposób jarzma nadają się wprost do budowy rdzenia, natomiast kolumny są dodatkowo przecinane wzdłużnie, a w miejsce przecięcia umieszcza się izolację, aby zmniejszyć prądy wirowe. Powstaje więc gotowy rdzeń symetryczny składający się z trzech walcowych kolumn i dwóch jarzm. Konstrukcję takiego rdzenia przedstawiono na rysunku 1.
Rdzenie zwijane wykorzystuje się do budowy transformatorów rozdzielczych. Budowa transformatorów mocy w takiej technologii jest niemożliwa, ponieważ nie można zbudować rdzenia pakietowanego o odpowiednich wymiarach, ze względu na zbyt małą szerokość taśmy amorficznej.
|
REKLAMA |
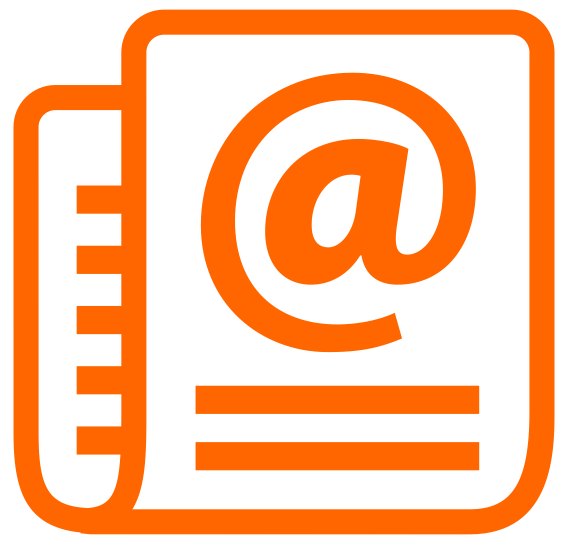

REKLAMA |