

Czujniki temperatury dla przemysłu – budowa, zastosowanie, działanie
Jednymi z kluczowych elementów współczesnej automatyki przemysłowej są inteligentne czujniki temperatury, połączone w czasie rzeczywistym z wysokowydajnymi sterownikami logicznymi poprzez zaawansowane interfejsy. To na nich w głównej mierze opiera się precyzyjna regulacja parametrów wielu dzisiejszych procesów technologicznych. Podstawowym celem takiej instalacji, opartej m.in. na tego typu czujnikach, jest stworzenie systemu całkowicie bezobsługowego, zdolnego do łatwej adaptacji i dostosowania swojego działania do każdych warunków oraz okoliczności.
Wszędzie tam, gdzie liczy się temperatura
Ogólnie rzecz ujmując, czujniki temperatury gromadzą informacje odnośnie temperatury konkretnego źródła lub wsadu, a następnie zmieniają je w postać możliwą do odczytania przez obserwatora lub odpowiednio przystosowane do tego urządzenie. Stosuje się je m.in. do pomiaru temperatury czynnika chłodzącego, a także olejów smarujących czy hydraulicznych. Sprawdzą się wszędzie tam, gdzie temperatura ma decydujące znaczenie dla prawidłowego funkcjonowania systemu przemysłowego lub w istotny sposób wpływa na zmianę przebiegu konkretnego procesu.
Element pomiarowy i osłona czujnika temperatury
Standardowe czujniki temperatury zbudowane są z elementu pomiarowego, znajdującego się w osłonie ochronnej, który umożliwia ich lokację bezpośrednio w środowisku/medium, a także z wbudowanego przyłącza procesowego (np. gwint, flansza montażowa lub wersja wtykana bez przyłącza procesowego) oraz przyłącza elektrycznego (kabel podłączeniowy, głowica przyłączeniowa, wtyczka). Ważnym kryterium podziału czujników temperatury jest kształt ich osłony, który wpływa na możliwości montażowe danego czujnika. Wbrew pozorom, jest to bardzo istotna kwestia, ponieważ czujniki o niedopasowanych do systemu gabarytach nie będą w stanie zmierzyć rzeczywistej temperatury. Znajdujący się we wnętrzu czujników bimetal, pod wpływem zmian temperatury, wygina się w określony sposób, a stopień tego wygięcia przekłada się na ruch wskazówki, która sygnalizuje zmierzoną temperaturę.
Sensor rezystancyjny i termopara
W automatyce przemysłowej najczęściej stosowanymi rozwiązaniami są czujniki RTD (rezystancyjne z ang. Resistance Temperature Device) lub termopary. Działanie czujników rezystancyjnych opiera się na zjawisku zmiany rezystancji elementu pomiarowego w funkcji temperatury (sposób tych zmian określony jest w tzw. charakterystyce termometrycznej danego elementu). Z kolei termopary wykorzystują zjawisko polegające na powstawaniu różnicy potencjałów. Pod wpływem różnicy temperatury między złączami (pomiarowym i odniesienia) powstaje różnica potencjałów.
Podstawowym elementem rezystancyjnych czujników temperatury, w tym m.in. popularnego modelu Pt100, jest rezystor o dużym współczynniku zmiany rezystancji wraz z temperaturą. W momencie spadku temperatury maleje również rezystancja (mniej Ω), a im temperatura jest wyższa, tym rezystancja wzrasta (więcej Ω). Cała konstrukcja wraz z rezystorem i przewodami została tak zbudowana, aby całe urządzenie pomiarowe zapewniało wysoką dokładność odzwierciedlającą rzeczywistą temperaturę w zakresie od ok. -50°C do 200°C (lub inne np. od -200°C do 600°C). „100” w nazwie modelu czujnika oznacza wartość znamionową oporności czujnika dla 0°C (czujnik Pt100 dla 0°C powinien mieć oporność 100 Ω).
Topowe czujniki temperatury dla przemysłu od JUMO
JUMO jest wiodącym światowym producentem czujników temperatury, które spełniają najwyższe wymagania w zakresie m.in. odporności chemicznej, krótkiego czasu reakcji, precyzji działania, odporności na wibracje, a także wymogi dotyczące procesów higienicznych. Przewagą marki JUMO nad konkurencją jest własna produkcja rezystorów do pomiaru temperatury, która odbywa się w pomieszczeniach czystych (cleanroom’ach). Wysoka precyzja oraz odpowiednie warunki produkcyjne gwarantują najwyższą jakość gotowych sensorów. Cienkowarstwowe czujniki JUMO Pt100, Pt1000 oraz Pt500, dostępne w różnych klasach dokładności B, A, 1/3B, 1/10B, to obecnie najchętniej wybierane sensory rezystancyjne na rynku, które znajdują swoje zastosowanie nie tylko w szeroko rozumianej automatyce przemysłowej, ale również w systemach i instalacjach codziennego użytku.
REKLAMA |
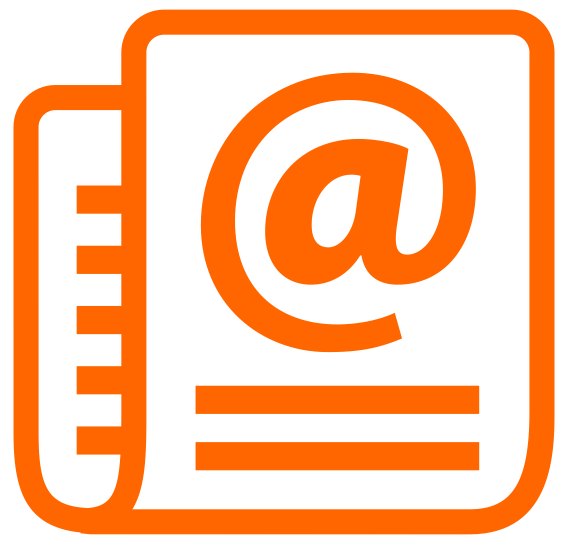
REKLAMA |