

Hydraulika na miarę Przemysłu 4.0 - czwartej rewolucji przemysłowej
Połączenie urządzeń hydraulicznych, elektrycznych i otwartych standardów komunikacji w rozwiązaniach sieciowych.
Połączenie produkcji przemysłowej z wirtualnym światem technologii informacyjnej w ramach koncepcji Przemysłu 4.0 nabiera coraz większego znaczenia. Wymagania stawiane technologiom automatyki są jasno zdefiniowane: zdecentralizowane inteligentne sterowanie i autonomiczne działanie, otwarte standardy komunikacji, szybkie łączenie w sieć i rozpoznawanie kontekstu w czasie rzeczywistym. W połączeniu z cyfrowymi technologiami sterowania i komunikacją zgodną z otwartymi standardami urządzenia hydrauliczne spełniają te wymagania. Taka kombinacja umożliwia także wykorzystanie w rozwiązaniach sieciowych potencjału urządzeń hydraulicznych: dużej gęstości mocy, modułowej konstrukcji i wydajności.
Wykonano już najważniejszy krok w procesie wprowadzania urządzeń hydraulicznych w erę Przemysłu 4.0: udało się połączyć siłowniki hydrauliczne z cyfrową elektroniką sterującą i przenieść funkcje sterowania na poziom oprogramowania. Technologie hydrauliczne są już całkowicie pokryte algorytmami zaimplementowanymi w oprogramowaniu, które automatycznie kompensują nieliniowe działanie napędów zbudowanych w tej technologii. Typowe sterowniki procesów, takich jak przejście ze sterowania ruchem na sterowanie siłą czy działanie synchroniczne, np. w prasach, są predefiniowane w fabrycznej konfiguracji oprogramowania. Zdecentralizowane inteligentne sterowanie umożliwia autonomiczne działanie napędów i ich samoczynną adaptację do zmiennych parametrów procesów.
Firma Bosch Rexroth jest jednym z głównych inicjatorów rozwoju na tym polu. Już na początku lat 90. nasi specjaliści w dziedzinie napędów i sterowania wprowadzili na rynek pierwsze elektrohydrauliczne osie liniowe ze zdecentralizowanym inteligentnym sterowaniem.
Szybkie łączenie w sieć dzięki oprogramowaniu
Firma Bosch Rexroth konsekwentnie podążała dalej tym szlakiem i stworzyła oprogramowanie uwzględniające dziesiątki lat jej doświadczenia.
– Nasze wiodące sterowniki są fabrycznie wyposażone w domyślne funkcje obsługi urządzeń hydraulicznych, tak że użytkownik może je bezpośrednio konfigurować – tak Markus Rukaber, dyrektor ds. zarządzania produktami firmy Bosch Rexroth, opisuje obecny stan techniki. „W ten sposób wspieramy użytkownika w uruchamianiu osi hydraulicznych”. Umożliwia to szybkie połączenie rozwiązań hydraulicznych z siecią informatyczną i ich optymalną kalibrację dla potrzeb konkretnych wymagań w trybie online.
Napędy ze zdecentralizowanym inteligentnym sterowaniem
Napędy pomp o zmiennej prędkości (Sytronix) oferują nowe możliwości w zakresie zdecentralizowanego inteligentnego sterowania. Łączą w sobie zalety urządzeń elektrycznych i hydraulicznych. Napędy Sytronix firmy Bosch Rexroth generują przepływ cieczy hydraulicznej odpowiednio do potrzeb i zmniejszają zużycie energii przez elementy hydrauliczne nawet o 80% w porównaniu z konwencjonalnymi rozwiązaniami. W zależności od zastosowania napęd Sytronix może nawet przejąć bezpośrednie sterowanie pozycją siłownika. Obniża to koszt systemu, zwiększa jego elastyczność i upraszcza rozruch.
Firma Bosch Rexroth idzie o krok dalej w swoich niezależnych osiach liniowych: te gotowe do podłączenia zespoły siłowników są zintegrowane z pompą o zmiennej prędkości. Siłownik generuje przemieszczenia liniowe bez strat i jest chroniony przed przeciążeniem. Niezależne osie instaluje się w taki sam sposób, jak napędy elektryczne. Wystarczy podłączyć kabel do zasilacza sieciowego, a oś do systemu sterowania.
– Te osie oferują wszystkie funkcje napędów elektrycznych, a z drugiej strony również wszystkie zalety urządzeń hydraulicznych, jak brak zużycia i duża gęstość mocy – mówi Markus Rukaber.
Podstawowe wymagania wobec otwartych standardów
Wszyscy eksperci zgadzają się, że Przemysł 4.0 wymaga ustandaryzowanych protokołów komunikacyjnych i języków programowania. Już teraz rozpowszechnione są systemy magistral typu fieldbus, łączących z systemem sterowania urządzenia działające w różnych technologiach, takie jak napędy elektryczne, urządzenia hydrauliczne i pneumatyczne. Wielu producentów maszyn poszło o krok dalej i zaczęło stosować protokoły komunikacji czasu rzeczywistego w sieciach Ethernet, takie jak sercos, Ethernet/IP czy PROFINET.
– Produkty Bosch Rexroth obsługują zarówno połączenia magistralowe, jak i połączenia czasu rzeczywistego z urządzeniami hydraulicznymi przez interfejsy Multi-Ethernet w napędach pomp o zmiennej prędkości i w sterownikach ruchu – podkreślił Markus Rukaber.
Interfejsy Multi-Ethernet firmy Bosch Rexroth obsługują w jednym urządzeniu wszystkie obowiązujące protokoły czasu rzeczywistego, takie jak sercos, EtherCAT, Ethernet/IP, PROFINET RT i VARAN. Dzięki temu systemy sterowania i systemy wyższych poziomów mają pełny dostęp do urządzeń hydraulicznych, co umożliwia integrację systemów niezależnie od tego, jakie firmy wyprodukowały poszczególne elementy.
Otwarte standardy dotyczą również programowania. Języki programowania sterowników PLC zgodne z normą IEC 61131 już stały się standardem w inżynierii mechanicznej i inżynierii produkcji. Przemysł 4.0 potrzebuje jednak czegoś więcej. Bosch Rexroth jest pierwszym producentem systemów sterowania, który połączył dziedziny automatyki i informatyki. Uhonorowana nagrodą HERMES (prestiżowa nagroda targów Hannover Messe) oraz Złotym Medalem AUTOMATICON 2014, technologia interfejsów Open Core Engineering umożliwia niezależne programowanie systemów sterowania firmy Bosch Rexroth w językach programowania wysokiego poziomu. Aby to osiągnąć, producent upublicznił rdzeń swoich systemów sterowania. W pierwszych powstających aplikacjach producenci maszyn zamiast na programowaniu sterowników PLC skoncentrowali się na wykorzystaniu smartfonów i tabletów do rozruchu, optymalizacji podczas pracy i diagnostyki swoich zastosowań.
Zdalna diagnostyka i monitorowanie warunków działania
Podłączenie urządzeń hydraulicznych do sieci Ethernet udostępnia wszystkie opcje ich zdalnej diagnostyki i zdalnej obsługi technicznej. Wszystkie elektroniczne układy sterowania są opatrzone niepowtarzalnymi identyfikatorami. Technicy posiadający odpowiednie uprawnienia mogą odczytywać dane niezależnie od miejsca pobytu i modyfikować parametry online.
Zdecentralizowane inteligentne sterowanie umożliwia także monitorowanie szeregu warunków działania urządzeń. Układy elektroniczne analizują sygnały z czujników, a oprogramowanie określa bieżący status roboczy systemu hydraulicznego. Jeżeli zmierzone wartości przekraczają zdefiniowany zakres tolerancji, system ostrzega operatora o zbliżaniu się do stanu krytycznego. Umożliwia to serwisantom podjęcie odpowiednich działań w już zaplanowanym oknie serwisowym, zanim maszyna się wyłączy.
Właściwości fizyczne napędów nieistotne dla systemu sterowania
Zdecentralizowane inteligentne sterowanie i otwarte standardy umożliwiają oprogramowaniu systemów hydraulicznych wykrywanie zmieniającego się kontekstu i automatyczne dostosowanie sekwencji przemieszczeń. Właściwości fizyczne napędu nie mają już znaczenia dla systemu sterowania wyższego poziomu. Nie jest istotne, czy przemieszczenie jest wywoływane elektrycznie, elektromechanicznie czy hydraulicznie. Oznacza to na przykład, że stacje pras hydraulicznych mogą odczytywać dane produktów z układów RFID i elastycznie dopasowywać działanie prasy do poszczególnych obrabianych przedmiotów bez konieczności angażowania operatora czy systemu sterowania wyższego poziomu.
W ten sposób urządzenia hydrauliczne dorównały urządzeniom elektromechanicznym i zaczęły spełniać wymagania Przemysłu 4.0. Dodatkowo oferują one niepowtarzalne zalety fizyczne.
– Urządzenia hydrauliczne wyposażone w układy elektroniczne i oprogramowanie, zgodne z otwartymi standardami, doskonale wpasowują się w obecne i przyszłe koncepcje Przemysłu 4.0 – potwierdza Markus Rukaber.
REKLAMA |
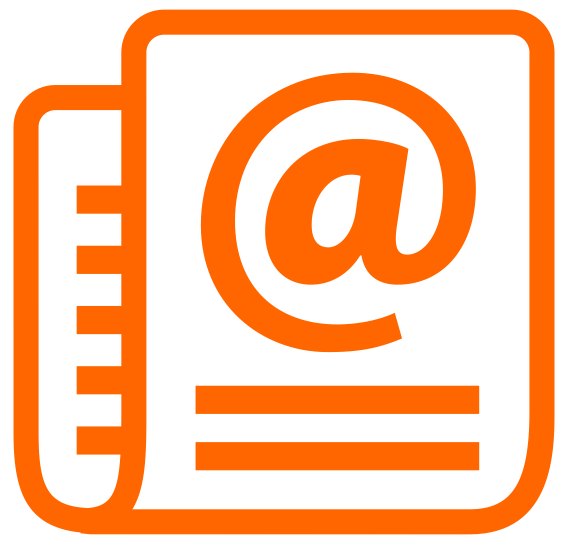
REKLAMA |
REKLAMA |