

Wywiad z Krzysztofem Pałganem - dyrektorem sprzedaży Dywizji Produkty i Systemy Energetyki, ABB
Podczas tegorocznych Międzynarodowych Targów Energetycznych ENERGETAB w Bielsku-Białej firma ABB zaprezentowała swoje propozycje w zakresie „Przemysłu 4.0”. O postępującej digitalizacji na rynku elektroenergetycznym rozmawialiśmy z dyrektorem sprzedaży Dywizji Produkty i Systemy Energetyki w firmie ABB, Krzysztofem Pałganem.
Panie Krzysztofie, Przemysł 4.0 kojarzy nam się przede wszystkim z inteligentnymi fabrykami i autodiagnostyką w procesach produkcyjnych. Jak wygląda i jakie przewagi niesie ze sobą cyfrowa rewolucja w sektorze elektroenergetycznym?
Krzysztof Pałgan: Zacznijmy od tego, że wśród największych wyzwań dla ludzkości wymienia się obecnie kilka tzw. megatrendów i powiązanych z nimi wyzwań, z którymi musi zmierzyć się współczesny świat. Pierwszą grupą są wyzwania wynikające z przeludnienia naszej planety, takie jak rosnące zapotrzebowanie na energię i deficyt surowców naturalnych. Kolejną kwestią są migracje ludności, widoczne zwłaszcza na obszarach odczuwających zmiany klimatyczne. Obok tych procesów jednym tchem wymienia się też trzecią grupę wyzwań, jaką niesie postępująca digitalizacja świata we wszystkich obszarach naszego życia – począwszy od bankowości, nowych aplikacji i produktów ułatwiających szybki dostęp do naszych zasobów.
Jeszcze 10 lat temu nowością i wielkim krokiem w kierunku digitalizacji był Internet of Things. Dzięki niemu mogliśmy już sterować przez „chmurę” różnymi gadżetami, np. włączyć za pośrednictwem telefonu ekspres do kawy, oświetlenie, rolety albo podlewanie roślin w ogrodzie. Dzisiaj staje się to normą, zwłaszcza dla młodego pokolenia, które zarządzanie poprzez aplikacje ma już we krwi i nie wyobraża sobie, aby jakimś urządzeniem nie można było sterować zdalnie. Kierunek tych zmian dostrzegalny był również w elektroenergetyce, gdzie globalne koncerny od pewnego czasu przygotowywały do cyfrowej rewolucji swoje zasoby ludzkie rozwijając produkty cyfrowe i kompetencje swoich pracowników. I choć takie cyfrowe rozwiązania były możliwe już nawet 20 lat temu, to rynek nie był wtedy jeszcze na to gotowy.
Z czego ten brak gotowości wynikał?
To był świat w którym tylko twarde miedziane druty elektryczne, sprężyna i mechanika oznaczały pewność wyłączenia – to dawało energetykom poczucie bezpieczeństwa, niezawodności i pewności, że zawsze kiedy pracownik podejdzie do urządzenia i osobiście załączy albo przekręci korbę, to mechanizm zadziała.
Pierwszy przełom w umysłach nastąpił właściwie już 30 lat temu, kiedy to zamiast zabezpieczeń elektromechanicznych zaczęły wchodzić układy elektroniczne. W miejsce zegarmistrzowskich dopasowań sprężyny i analogowych pomiarów prądu czy napięcia, weszła elektronika. Producenci zdawali sobie sprawę w jakim kierunku zmierza świat i przygotowywali się do cyfrowej rewolucji. Za wprowadzaniem Industry 4.0 lobbowano już 10 lat temu, ale dopiero dzisiaj wyraźnie widać, że energetyka i odbiorcy przemysłowi są bardziej świadomi. Wyrosło pokolenie, które jest w stanie tę technologię zrozumieć, przyjąć i zaaplikować, a przede wszystkim dostrzec płynące z niej korzyści. I stąd pojawiają się na rynku europejskim pierwsze takie „rodzynki” jak prezentowane na naszym stoisku hybrydowe rozdzielnice PASS dla stacji cyfrowych, które zamówione zostały niedawno przez Deutsche Bahn. W takim module (wyłącznik wysokiego napięcia – red.) energetycy czują się pewnie kiedy to naciągnięta sprężyna będąca zasobnikiem energii jest w każdej chwili gotowa do wyłączenia awaryjnego. Tutaj funkcję tę przejmuje silnik elektryczny, który w danym momencie wymaga dostarczenia energii elektrycznej z jakiegoś źródła, np. akumulatora czy kondensatora.
A co jeśli by się okazało, że taki akumulator nie będzie gotowy dostarczyć energii akurat w momencie awarii?
Gdyby na stacji elektroenergetycznej zabrakło napięcia pomocniczego do ładowania tej baterii to wyłącznik oczywiście nie zadziała, ale zastanówmy się: jeżeli nie ma napięcia pomocniczego na rozdzielni elektrycznej, która ma zarządzać rozdziałem energii to przecież i tak nic nie działa!
W stacji cyfrowej (ang. digital substation) pomiary nie odbywają się w sposób analogowy poprzez przekładniki, lecz z wykorzystaniem światłowodów. Również komunikacja na tej stacji i wymiana informacji pomiędzy przekaźnikami odbywa się w sposób cyfrowy zgodny z nowym protokołem 61850 (protokół wymiany informacji ustalony przez wiele koncernów jako konsensus), więc niezależnie od producenta urządzenia te mogą się ze sobą komunikować i wzajemnie „rozumieć”. To jest duży przełom i powoli do mentalności młodszych pokoleń to przemawia.
Tauron Dystrybucja – jako pierwszy w Polsce i pionier w Europie – ogłosił w tym roku przetarg na rozdzielnię 110 kV w pełnym układzie H w konwencji cyfrowej i my (ABB – red.) ten przetarg wygraliśmy. Widać, że idea Industry 4.0 już przenika do świadomości w elektroenergetyce. Podobnie w przemyśle – żeby być konkurencyjnym na rynku, musi być zapewniona pewna jakość, powtarzalność produktów i niskie koszty produkcji. Robotyzacja postępuje bardzo szybko. W Polsce mamy małe nasycenie robotami, ale to będzie się szybko zmieniać. Zachowanie ciągłości produkcji, czyli też jakość mediów potrzebnych do wytworzenia produktów musi być najwyższa, bez żadnych przerw, po prostu niezawodna. Dlatego monitorowanie poprawności działania czy stanu fizycznego zasilających urządzeń staje się realną potrzebą.
Jednocześnie zaczynamy mówić o tym, aby w Industry 4.0 urządzenia same się monitorowały, wysyłały informacje w chmurę i dzieliły się tymi danymi z producentami, aby mogli szybko zareagować albo poprawić jakość następnego produktu, który za chwilę wejdzie w użytkowanie. I takie rozwiązania już widzimy, np. w motoryzacji, gdzie wprowadzane są auta, które online dostarczają producentowi dane o tym jak się sprawuje silnik. Dzięki temu możemy np. dostać informację, że znaleziono usterkę i 10 tys. samochodów z danej partii jest do wymiany.
Jakiego typu dane z urządzeń możemy przetwarzać i analizować w przemysłowym Internecie Rzeczy?
To są zawsze dane wtórne, najlepiej posłużyć się prostym przykładem. Wyobraźmy sobie rafinerię, w której mamy silniki elektryczne napędzające setki albo tysiące układów różnych pomp, turbosprężarek itd. W ubiegłym roku na targach w Hanowerze ABB pochwaliło się niewielkim urządzeniem do monitorowania stanu silnika – ABB Ability ™ Smart Sensor, które łatwo możemy przymocować do każdego silnika, aby mierzyło nam jego temperaturę, drgania czy wibracje łożyska. Bazując na tych danych potrafi ocenić jak pracuje dany silnik i przewidzieć czy nie ulegnie on wkrótce awarii. Udostępniając te informacje online i wysyłając je do właściwego systemu, można zapobiec awarii poprzez wyłączenie fragmentu linii w sposób planowy, aby wymienić wadliwe urządzenie i nie doprowadzić do dłuższej, nieplanowanej i bardziej kosztownej przerwy.
W energetyce zawodowej głównym wskaźnikiem jakości firmy dystrybucyjnej jest czas trwania przerw w dostawie energii, a więc czas potrzebny do przywrócenia napięcia i częstotliwość występowania tych przerw. Urząd Regulacji Energetyki rozlicza zakłady energetyczne właśnie z tych wskaźników. Zbierając dane o pracy urządzeń, np. temperaturę transformatora, stan i skład oleju, czy zawarte w nim gazy, możemy zapewnić jak najkrótszy łączny czas przerw oraz ograniczyć ich ilość poprzez zapobieganie awarii.
Z drugiej strony gromadzenie tych wszystkich wrażliwych danych w chmurze może być bardzo niebezpieczne. Kwestia cyberbezpieczeństwa jest szczególnie ważna w energetyce, gdzie mamy do czynienia z infrastrukturą krytyczną, która może być celem ataków hackerskich. Czy ABB jest przygotowana na takie zagrożenia?
Zdecydowanie, równolegle do rozwoju tego rodzaju technologii musi następować postęp w odporności na wszelkiego rodzaju ataki hackerskie, nawet te najprostsze. Przykładem może być zablokowanie działania jakiegoś urządzenia poprzez wysłanie do niego setek tysięcy sygnałów. Dlatego wszystkie produkty z cyfrowej oferty ABB podlegają odpowiednim procedurom i przechodzą testy na cyberzagrożenia.
Producenci muszą dbać o to, żeby dostęp do ich urządzeń odbywał się w sposób ściśle kontrolowany. Ale użytkownicy obawiają się nie tylko ataków zewnętrznych. W przemysłowym Internecie Rzeczy mamy do czynienia z udostępnieniem producentom w chmurze danych z urządzeń po to, abyśmy mogli usprawniać nasze produkty i procesy je obsługujące. I to jest dla nas kolejna bariera do pokonania – przekonanie użytkownika, który godzi się na taką współpracę, że jego dane będą bezpieczne. Klienci obawiają się, że gdyby takie dane wyciekły, mogłyby posłużyć konkurencji do analizy całych procesów produkcyjnych, usprawniania organizacji pracy itd. Oczywiście odbywa się to zawsze pod kontrolą, musimy zapewnić bezpieczeństwo danych, ale nie ukrywam, że taka psychiczna bariera występuje.
W tym wszystkim musimy zachowywać się bardzo roztropnie i nie wyprzedzać rzeczywistości, bo już 20 lat temu były dostępne rozwiązania, które trochę wyprzedziły ówczesne realia. Mieliśmy urządzenia smart gdzie wszystko obywało się drogą cyfrową, czy moduły na najwyższe napięcia, które monitorowały urządzenia. Ale wtedy świat nie był gotowy na przyjęcie tych wszystkich danych i taki skok cywilizacyjny.
Czyli nie tylko lobbing ze strony producentów, ale też pewna gotowość pokoleniowa wprowadziły Przemysł 4.0 na rynek?
Myślę że to wynika przede wszystkim ze zmiany pokoleniowej. Ludziom, którzy dzisiaj kończą szkoły, dużo łatwiej to wszystko zrozumieć i zaakceptować. Ponadto świadomość zachowania tego bezpieczeństwa, dostępności urządzeń i ich sprawności doprowadziła do tego, że obecne systemy są doskonalsze i zapewniają to czego 20 lat temu wymagaliśmy, a obawialiśmy się wprowadzić.
Musimy też uważać, żeby nie przesadzić z tą całą „cyfrowością”. Tak naprawdę Industry 4.0 oraz technologie cyfrowe powinny nam upraszczać życie, a nie komplikować. Nie można czegoś robić na siłę tylko dlatego, że wchodzimy teraz w nowy, cyfrowy świat. Musimy być na to mentalnie przygotowani.
Chwalą się Państwo, że już ponad połowa oferowanych przez ABB wyrobów jest powiązanych z oprogramowaniem i cyfrową obsługą. W energetyce widzimy już te „rodzynki”. A które branże przodują w zastosowaniu rozwiązań cyfrowych?
Przemysł samochodowy, spożywczy i w zasadzie każdy, w którym następuje robotyzacja. I wyróżniamy tutaj dwa obszary. Pierwszy obejmuje przemysł, który wykorzystując technologię cyfrową chce poprawić swoje warunki konkurencyjności, obniżyć koszty pracy, wytworzyć tanio swoje produkty. A więc podejście typowo biznesowe.
Jest też drugi obszar związany bardziej z bezpieczeństwem pracy systemów i urządzeń dla całych krajów. Mówimy tu o energetyce, źródłach energii, przemyśle ciężkim i chemicznym, a więc strategicznych segmentach przemysłu.
Czyli konkurencyjność i bezpieczeństwo – to są te parametry, które napędzają wykorzystywanie nowoczesnych, cyfrowych rozwiązań i w tych dwóch obszarach należy szukać liderów. Energetyka, której priorytetami są zapewnienie bezpieczeństwa energetycznego i poprawienie niezawodności funkcjonowania urządzeń jest naturalnym uczestnikiem tego rynku.
Na targach w Bielsku prezentują Państwo też szybką i uniwersalną ładowarkę Terra 53 CJG dla pojazdów elektrycznych. Obecnie jesteśmy świadkami przyspieszenia na rynku EV. W jakim kierunku będzie rozwijać się rynek i oferta ABB dla elektromobilności?
Zupełnie różnie to będzie się rozwijać w różnych krajach. W najbliższym dziesięcioleciu będziemy obserwować zdecydowane przyspieszenie tego procesu, ale my już jesteśmy na to gotowi, mamy różne systemy ładowania: prądem przemiennym, prądem stałym – dla Lidla, stacji benzynowych, sklepów wielkopowierzchniowych, do użytku własnego, lub dla transportu publicznego – mamy różne ładowarki i jesteśmy na to przygotowani. Jednak nie tylko same ładowarki mają znaczenie, ale także zarządzanie całą siecią ładowania, sposób rozliczania opłat, monitorowanie jakości pracy, pewności zasilania. To wszystko jest powiązane całym oprogramowaniem, które my również dostarczamy. Kiedy się spojrzy na te wszystkie elementy hardwarowe to ciężar odpowiedzialności przesuwa się z fizycznego urządzenia na software i zarządzanie tym urządzeniem. To się wpisuje w trend ABB Ability™, który mówi, że jesteśmy gotowi do pozyskiwania i analizy danych ze wszystkich urządzeń.
A kiedy Pana zdaniem ładowarki wejdą „pod strzechy” i będą np. standardowym wyposażeniem na parkingu każdego nowego bloku?
Tak naprawdę na całym świecie zależy to od regulacji prawnych. Albo państwa będą inicjować rozwój poprzez dofinansowanie użytkowników końcowych aut albo dofinansowywać całą infrastrukturę. Bo kiedy będzie dużo użytkowników końcowych, to infrastruktura będzie musiała sama się dostosować. Z drugiej strony, kiedy będzie dostępna szeroko infrastruktura, to wola i chęć posiadania elektrycznego auta, które można wszędzie naładować też będzie większa. I różne rządy z tym różnie postępują: w Niemczech dofinansowuje się użytkowników końcowych, w Polsce podchodzimy do tego z drugiej strony – zainicjowania tego procesu od strony infrastruktury.
Dziękuję za rozmowę.
REKLAMA |
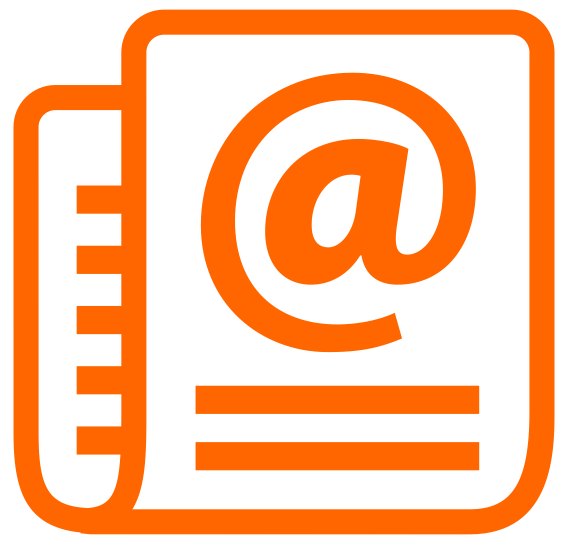

REKLAMA |