

Zrobotyzowane spawanie – przegląd aktualnych rozwiązań
Zrobotyzowane stanowiska do realizacji procesów spawania składają się z dwóch podstawowych elementów: robota przemysłowego oraz źródła spawalniczego. Robot przemysłowy odpowiada za przenoszenie narzędzia po zadanej trajektorii. Realizuje w ten sposób spawanie w odpowiednich miejscach elementu spawanego.
Źródło spawalnicze odpowiada za proces i parametry spawania. Od rodzaju źródła spawalniczego zależy metoda spawania. Na jakość spawania wpływa zarówno źródło, jak i robot. Źródło wpływa na jakość spawania bezpośrednio – poprzez parametry prądowe i napięciowe, odpowiedni timing oraz precyzyjne podawanie materiału. Robot wpływa na jakość spawania pośrednio – przez precyzję prowadzenia fajki spawalniczej i stabilność ruchów.
Roboty spawalnicze - trendy w robotyce
Spawanie jest jednym z podstawowych zastosowań robotów przemysłowych. Specyficzny charakter pracy tych robotów spowodował, że zostały opracowane specjalne konstrukcje ramion robotów oraz kontrolery i oprogramowanie. Konstrukcje te są ciągle modyfikowane i ulepszane, aby jak najlepiej odpowiadały potrzebom przemysłu.
Przykładowe systemy spawalnicze | |||
System | Opis | ||
TPS 5000 | Zaawansowany, wszechstronny system do spawania MIG/MAG stali i metali nieżelaznych (miedź, aluminium), również do lutospawania. | ||
CMT | System spawania oparty na technologii CMT (Cold Metal Transfer): bezodpryskowe, super-stabilne spawanie materiałów o mniejszych grubościach, z wyjątkowo niskim wprowadzaniem ciepła. Źródło CMT można również wykorzystać jako standardowe źródło TPS | ||
TIG | Stanowisko do spawania w metodzie TIG z podawaniem drutu zimnego | ||
TransSteel | Prosty, choć nowoczesny system spawania MIG/MAG, stworzony z myślą o powszechnym wykorzystaniu w standardowych aplikacjach spawania stali czarnej. |
Aktualnie widać wzrost zainteresowania robotami spawalniczymi o mniejszych udźwigach (do 6 kg). Wynika to z obniżenia wagi osprzętu spawalniczego. Oczywiście w ofercie dostawców robotów przemysłowych są również roboty o większych udźwigach (np. Kawasaki RA010L o udźwigu 10 kg lub Kawasaki RA020N – o udźwigu 20 kg). Roboty o większych udźwigach wymagane są do realizacji procesów z wykorzystaniem cięższego osprzętu: spawanie z wykorzystaniem podwójnej fajki (twin, tandem) lub gdy robot oprócz fajki spawalniczej ma przenosić dodatkowe czujniki. Zauważamy również wzrost zainteresowania robotami o dużych zasięgach. Firma Kawasaki wprowadziła do swojej oferty robota RS015X, który ma zasięg 3150 mm. Rozwiązanie takie pozwala na spawanie dużych obiektów bez konieczności zastosowania torów jezdnych.
Od pewnego czasu wymogiem stawianym robotom spawalniczym jest możliwość łatwej rozbudowy o dodatkowe osie (pozycjonery, obrotniki, tory jezdne). Tendencja, który dotyczy robotów przemysłowych w każdym zastosowaniu, to wzrost prędkości pracy, dyktowany chęcią wzrostu wydajności.
Obecnie bardzo istotne są możliwości komunikacyjne robota przemysłowego. Od tego zależy, czy będzie w stanie współpracować z wybranym źródłem spawalniczym.
Rynek w praktyce zweryfikował rozwiązanie polegające na możliwości prowadzenia przewodów wewnątrz kiści robota (hollow wrist – przelotowy nadgarstek). Rozwiązanie mające jako główną zaletę zabezpieczenie przewodów oraz ograniczenie możliwości kolizji, okazało się częstokroć niepraktyczne. Kiedy w aplikacji wymagane jest przezbrajanie robota lub wymiana przewodów doprowadzających media do narzędzia, przelotowy nadgarstek w ogóle się nie sprawdza. Zastosowanie hollow wrist wydłuża znacząco czas potrzebny na przezbrojenie, co zmniejsza wydajność stanowiska.
Przegląd procesów i technologii spawalniczych
Podobnie jak roboty przemysłowe, również technologia spawalnicza ma swoją historię, w której motywem przewodnim jest ciągły rozwój. Już w latach 50-tych dwudziestego wieku wprowadzono na rynek pierwszy transformator spawalniczy firmy Fronius z regulacją magnesu w obejmie, umożliwiającego płynną regulację prądu spawania. Dało to początek dużej rodzinie rozwiązań spawalniczych firmy Fronius. Kolejnym krokiem milowym było przedstawienie światu, w 1981 roku, pierwszego zasilacza inwerterowego z taktowanym obwodem pierwotnym. Technologia inwertorowa otwiera nieznane dotychczas możliwości w technologii spawania. W 1998 roku Fronius zaprezentował pierwsze, w pełni cyfrowe, synergiczne źródła prądu spawalniczego MIG/MAG (TransSynergic 4000 / 5000; TransPuls Synergic 2700 / 4000 / 5000). Pozwoliło to uzyskać pełną powtarzalność procesu, gwarantując najwyższą jakość spawania manualnego i zrobotyzowanego.
Zrobotyzowane spawanie z robotem Kawasaki FA006E
z pozycjonerem dwuosiowym w technologii CMT
Równolegle do rozwoju źródeł manualnych, trwają prace nad osprzętem spawalniczym dla robotów przemysłowych. Aktualnie precyzyjne roboty oraz najwyższej jakości osprzęt spawalniczy pozwalają realizować pełną gamę procesów spawalniczych dla różnego rodzaju materiałów.
Spawanie zawsze było jednym z głównych zastosowań robotów przemysłowych. Ich wykorzystanie w procesie produkcji pozwalało na uzyskanie produktów spełniających najwyższe wymagania, jednocześnie gwarantując bardzo dużą wydajność. Dziś, dzięki rozwojowi techniki, obsługa robotów jest dużo prostsza. Rozwój inteligentnych źródeł spawalniczych pozwala w prosty sposób zapanować nad procesem spawania. Ceny zakupu sprzętu oraz integracji znacząco spadły i są przystępne nawet dla małych przedsiębiorstw. Inwestycja w zrobotyzowane spawanie jest z pewnością opłacalna i coraz częściej konieczna w celu zapewnienia odpowiedniej jakości produktów oraz konkurencyjności przedsiębiorstw na europejskim rynku.
REKLAMA |
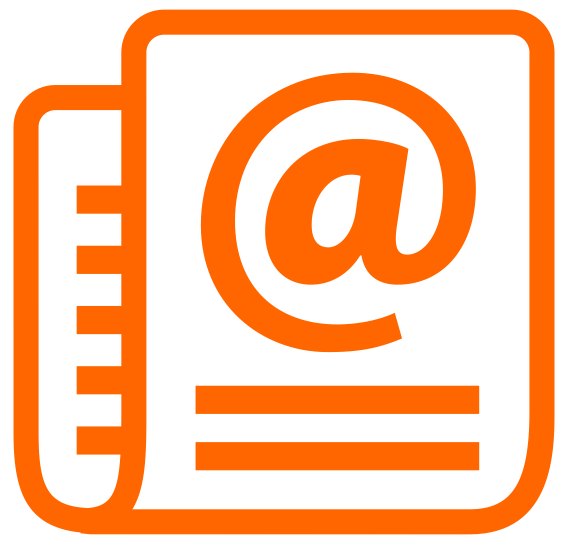
REKLAMA |
.eu/pl/pl</a> i sami oceńcie.