

Zrobotyzowana produkcja szkła
Jako specjalista w budowie kompletnych obiektów przemysłowych w zakresie wytwarzania szkła metodą float (proces Pilkingtona) lub szkła płaskiego, firma HEGLA stawia na roboty przemysłowe firmy Kawasaki.
Produkcja szkła w metodą float jest delikatnym procesem, i to nie tylko ze względu na ryzyko stłuczenia produktu, które, zgodnie z panującym przekonaniem, przynosi szczęście. Największa trudność polega na tym, aby produkcja przebiegała w ciągłym, nieprzerwanym procesie.
W produkcji roztopiona masa szklana o temperaturze 1100°C zostaje wprowadzona do kąpieli cynowej (temperatura topienia 232°C), w której znacznie lżejsza masa unosząc się, aż do całkowitego wychłodzenia, zostaje przetransportowana dalej. Stąd wywodzi się również nazwa tej metody produkcji szkła (ang. to float = pływać). Obszar wprowadzania nazywany jest gorącym końcem, a obszar wyprowadzania masy – zimnym końcem. Szkło przechodzi w tej drodze przez piec wygrzewający, jest odprężane i wychładzane, następnie kontrolowane i wielokrotnie przycinane do pożądanych wymiarów. Wymiary wyjściowe po pierwszym cięciu wynoszą przy tym 6000x3210 mm. W procesie tym mogą powstawać szkła o grubości od poniżej 1 mm do 24 mm.
Firma HEGLA w procesie produkcji szkła specjalizuje się i przygotowuje obszar za zimnym końcem. Buduje przenośniki i urządzenia do cięcia, jak również systemy buforowania i magazynowania. Na tym etapie stosuje się roboty firmy Kawasaki, które niezawodnie i nieprzerwanie odbierają szyby szklane z urządzenia.
Dla firmy Cardinal, amerykańskiego producenta szkła w procesie float, zostało wykonane urządzenie z wieloma wyjściami bocznymi, łącznie z urządzeniami do przycinania i łamania szyb. Przenoszenie tafli szkła przejęły po dwa roboty Kawasaki typu ZX165U z każdej strony. Są one odpowiedzialne za pobranie tafli szkła o odpowiednich dla klienta wymiarach. Z pomocą dopasowanych chwytaków i przy wykorzystaniu techniki próżniowej podnoszą one szklane tafle z przenośnika (bez jego zatrzymywania) i układają je na przygotowanych wcześniej stojakach. Stojaki umieszczone są na stołach obrotowych, tak że mogą być zmieniane przez obrót o 180°. Także tutaj – jak w całym procesie produkcji szkła metodą float – najważniejsze jest zapewnienie ciągłości produkcji.
– Często jest tak, że tafla szklana może być chwycona tylko na dolnej stronie, tzw. stronie cynowej, po to, by uniknąć zabrudzeń na wierzchniej stronie. Wierzchnie strony tafli są najczęściej dodatkowo pokrywane w późniejszej obróbce i wymagane jest zapewnienie najwyższej czystości. Dlatego chwytamy taflę od spodu wsuwając chwytak przez otwór w podajniku i wyciągamy ją z urządzenia nie przerywając jego pracy – mówi Stefan Reuter, jeden z konstruktorów tego urządzenia i kierownik działu inżynierów w firmie HEGLA.
Proces wsuwania chwytaka od spodu był wielkim wyzwaniem, przed jakim chętnie stanęli inżynierowie. Sercem jest podajnik o określonym rozstawie rolek, pomiędzy którymi chwytak może złapać taflę od spodu. Robot porusza się w tym celu z prędkością ruchu taśmy, jednocześnie chwytając taflę i podnosząc ją z taśmy. Dzięki specjalnie skonstruowanemu otworowi w taśmie robot Kawasaki ZX165U może po podniesieniu tafli z taśmy bezproblemowo opuścić obszar podajnika.
Aby proces ten przebiegał sprawnie robot wyposażony jest w dodatkową opcję, tzw. „Conveyer Tracking" – śledzenie ruchu taśmy. Funkcja ta umożliwia całkowitą synchronizację robota z przenośnikiem, co umożliwia maksymalnie delikatne pobranie tafli z pracującej maszyny.
Enkoder zamontowany na początku podajnika określa posuw. Równocześnie czujnik rejestruje aktualną pozycję tafli szklanej. Obydwie te informacje wykorzystywane są przez sterowanie robota do tego, aby określić aktualną pozycję pobrania tafli szkła i podążać za nią. Wynikła z tego funkcja pobierania tafli szklanej w trackie pracy taśmy jest rozwiązaniem koniecznym do stosowania w procesach ciągłych oraz na bardzo wydajnych liniach produkcyjnych.
Tafle szklane są na początku podajnika tak ustawione, że robot zawsze zna dokładną pozycję ich pobrania i może je sprawnie i w uporządkowany sposób układać na stojakach. W celu dokładnego ustawienia tafli na stojakach robot podjeżdża dodatkowo do wcześniej zdefiniowanego narożnika tafli, podnosi i dosuwa ostrożnie do odpowiedniej pozycji. Do aktywnego wyrównywania tafli szkła zainstalowano specjalną krawędź pozycjonującą na chwytaku, która służy jako punkt odniesienia.
Wymiary tafli szklanych w tym urządzeniu zmieniają się od 500 x 500 mm do 2450 x 1850 mm, przy grubości od 2,2 do 6 mm, Ciężar tafli wynosi przy tym od 1,4 do 70 kg. Do pobierania różnych wymiarów szyb służą tylko dwa rodzaje chwytaków, które w robotach Kawasaki ZX165U są w miarę potrzeb automatycznie zmieniane. Czas cyklu wynosi 12 do 18 sekund, w zależności od wymiarów danej tafli.
Waga chwytaka razem z szybą waha się znacząco i może osiągnąć maksymalny udźwig Kawasaki ZX165U. Z tego powodu inżynierowie Kawasaki opracowali specjalną procedurę dopasowania parametrów ruchu do zwiększonego udźwigu. Jest to możliwe ponieważ robot ZX165U (udźwig 165 kg) i ZX200U (udźwig 200 kg) mają tą samą konstrukcję mechaniczną, różnią się jedynie parametrami ruchu. Procedura ta polega na dynamicznej zmianie parametrów ruchu (maksymalne prędkości, przyśpieszenia) w zależności od masy aktualnie pobieranej szyby. Możliwe to było dzięki współpracy inżynierów Kawasaki z integratorem, którzy wspólnie opracowali rozwiązanie głęboko ingerujące w sterowanie robota. Dzięki temu możliwe stało się automatyczne stosowanie różnych ustawień w systemie sterowania robota, tak aby zgodnie z potrzebami mógł pracować z obciążeniami 165 do 200 kg. Minimalizuje to zużycie i gwarantuje długie funkcjonowanie robota przy maksymalnej wydajności.
Duże zróżnicowanie wymiarów i wagi tafli szkła oraz wymagania funkcjonalne (pobieranie szyb bez zatrzymywania transportera, duża wydajność) uniemożliwiałyby realizacje zadania w inny sposób niż przy pomocy robotów.
Uwzględniając teoretyczny koszt 1-2 pracowników na zmianę oraz oprzyrządowanie i przeszkolenie, inwestycja zwraca się w ciągu 2-3 lat. Jednakże obciążenie pracą byłoby zbyt wysokie, aby zagwarantować ciągłość procesu przy pracy manualnej. Jest to idealne zadanie dla robotów Kawasaki X165U, które gwarantują ciągłość pracy w każdych warunkach. a dodatkowy aspekt bezpieczeństwa, zapewniony przez roboty, również przynosi wymierne zyski.
Opracowane na podstawie materiałów KRG
REKLAMA |
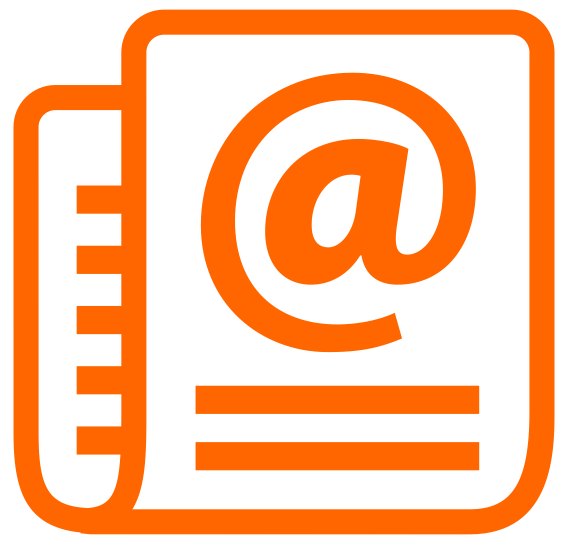

REKLAMA |