

Jak dostosować ciśnienie w agregacie do malowania różnych powierzchni?
Zbyt wysokie ciśnienie może prowadzić do nadmiernego zużycia farby, a zbyt niskie – do nierównomiernego krycia i zatykania dyszy. Właściwe ustawienie parametrów roboczych agregatu malarskiego ma bezpośredni wpływ na jakość powłoki i efektywność pracy. W tym poradniku omawiamy, jak dobrać ciśnienie do różnych powierzchni, by uzyskać optymalne rezultaty.
Ciśnienie robocze w agregacie malarskim
Ciśnienie robocze w agregacie malarskim decyduje o charakterystyce rozpylania farby, a tym samym – o końcowym efekcie wizualnym i trwałości powłoki. Od jego prawidłowego ustawienia zależy nie tylko równomierność krycia, ale też zużycie materiału, tempo pracy i ryzyko powstawania defektów, takich jak zacieki, mgła natryskowa czy niedomalowania.
W przypadku aplikacji hydrodynamicznej, gdzie farba rozbijana jest wyłącznie siłą ciśnienia, nawet niewielkie odchylenia od optymalnego zakresu mogą mieć zauważalne skutki. Zbyt wysokie ciśnienie prowadzi do nadmiernego rozpylenia cząsteczek, co zwiększa straty materiałowe i może powodować rozbryzgi na krawędziach. Z kolei ciśnienie zbyt niskie skutkuje niewystarczającym rozdrobnieniem farby, zaburzoną strukturą natrysku i problemami z płynnością pracy urządzenia.
Agregaty do malowania umożliwiają precyzyjną regulację parametrów, jednak ich skuteczne wykorzystanie wymaga zrozumienia zależności między ciśnieniem a typem powierzchni oraz właściwościami medium. Dopiero świadome zarządzanie tymi zmiennymi pozwala uzyskać profesjonalne rezultaty i zoptymalizować proces malowania w warunkach warsztatowych oraz na placu budowy.
Czynniki wpływające na ustawienie ciśnienia w agregacie
Ustawienie ciśnienia w agregacie malarskim nie jest wartością uniwersalną – zależy od szeregu zmiennych, które wpływają na jakość natrysku i efektywność pracy. Pierwszym z nich jest rodzaj malowanej powierzchni. Gładkie, twarde materiały, takie jak metal czy szkło, wymagają innego ustawienia ciśnienia niż powierzchnie porowate, jak drewno, beton czy tynk. W przypadku tych ostatnich, wyższe ciśnienie pomaga w uzyskaniu gładszej powłoki i skuteczniejszym wypełnieniu nierówności.
Kolejnym czynnikiem jest rodzaj farby. Farby wodne lub lateksowe, które mają mniejszą lepkość, wymagają mniejszego ciśnienia w porównaniu do farb olejnych, które są bardziej gęste. Zbyt niskie ciśnienie przy gęstszych farbach może skutkować niewłaściwym rozpyleniem, a co za tym idzie – nierównomiernym pokryciem powierzchni. Z kolei farby rozcieńczone wymagają ustawienia wyższego ciśnienia, aby zapewnić równomierne rozpylenie.
Wielkość dyszy agregatu również wpływa na ustawienia ciśnienia. Mniejsze dysze wymagają wyższego ciśnienia, aby zapewnić odpowiednią prędkość rozpylania, podczas gdy większe dysze pozwalają na używanie niższego ciśnienia bez utraty jakości aplikacji.
Ostatnim czynnikiem jest odległość pomiędzy dyszą a powierzchnią malowaną. Im dalej znajduje się dysza od powierzchni, tym wyższe ciśnienie jest wymagane, aby utrzymać równomierny rozkład farby.
Jakie ciśnienie agregatu do malowania gładkich powierzchni?
Malowanie gładkich powierzchni wymaga precyzyjnie dobranego ciśnienia, które umożliwi równomierne rozpylanie farby bez efektu zacieków, prześwitów czy rozbryzgów. W przypadku ścian szpachlowanych, płyt kartonowo-gipsowych, sufitów czy elementów metalowych, zalecane ciśnienie robocze mieści się zazwyczaj w zakresie od 110 do 160 barów – w zależności od rodzaju farby i średnicy użytej dyszy.
Przy zastosowaniu farb lateksowych lub akrylowych o średniej lepkości, skuteczna praca agregatu wymaga ciśnienia w granicach 120–140 barów. W przypadku farb gruntujących lub rzadszych powłok nawierzchniowych wartości te można obniżyć do około 110 barów. Z kolei przy farbach gęstszych, zwłaszcza w systemach bezpowietrznych, konieczne może być zwiększenie ciśnienia do 150–160 barów, szczególnie przy dyszach o większym otworze.
Zbyt wysokie ciśnienie na gładkiej powierzchni może prowadzić do powstawania zbyt cienkiej warstwy, nadmiernej mgły natryskowej i strat materiału. Z kolei zbyt niskie – do niedokładnego pokrycia i efektu „skórki pomarańczy”. Dlatego każdorazowo warto przeprowadzić próbę natrysku na fragmencie podłoża, by zweryfikować rozkład farby i dostosować parametry do warunków rzeczywistych.
Jakie ciśnienie agregatu do gęstych farb?
Gęste farby stawiają agregatowi znacznie większy opór niż powłoki o rzadkiej konsystencji – wymagają więc odpowiednio wyższego ciśnienia, by zapewnić prawidłowe rozdrobnienie i równomierny natrysk. Niedostosowanie parametrów może skutkować przerywaną pracą, zacinaniem się dyszy lub wyraźnie nierównomiernym pokryciem powierzchni.
W przypadku farb olejnych, akrylowych o dużej gęstości, lakierów dwuskładnikowych czy mas strukturalnych stosowanych w technikach dekoracyjnych, zaleca się ustawienie ciśnienia w przedziale od 160 do nawet 220 barów – w zależności od lepkości materiału i typu zastosowanej dyszy. Warto przy tym pamiętać, że do pracy z gęstymi farbami niezbędne jest nie tylko odpowiednie ciśnienie, ale też filtracja – drobne zanieczyszczenia mogą łatwo zatkać dyszę. Regularna kontrola parametrów i próby aplikacyjne na odpadowym fragmencie podłoża pozwolą uniknąć błędów oraz zoptymalizować zużycie materiału.
Testowanie i korekta ciśnienia roboczego agregatu w trakcie pracy
Skuteczne testowanie i korekta ciśnienia roboczego w trakcie malowania pozwalają uniknąć typowych błędów aplikacyjnych i utrzymać stałą jakość natrysku. Kluczowe jest szybkie rozpoznanie objawów wskazujących na nieprawidłowe ustawienie parametrów. W praktyce warto zwrócić uwagę na:
rozbryzgi i nadmierną mgłę natryskową – mogą świadczyć o zbyt wysokim ciśnieniu; warto stopniowo je obniżać, obserwując rozkład farby,
efekt „skórki pomarańczy” lub niedomalowania – często wskazuje na zbyt niskie ciśnienie; zalecane jest zwiększanie ciśnienia w niewielkich krokach,
zatykanie się dyszy lub przerywany strumień – może oznaczać zbyt gęsty materiał przy niedostatecznym ciśnieniu lub nieodpowiedni filtr.
Testy warto przeprowadzać na fragmencie powierzchni poza docelową strefą malowania. Korektę ciśnienia należy łączyć z kontrolą stanu dyszy, filtra i odległości od podłoża. Prawidłowa regulacja w czasie pracy pozwala uniknąć przerw technologicznych i strat materiałowych.
REKLAMA |
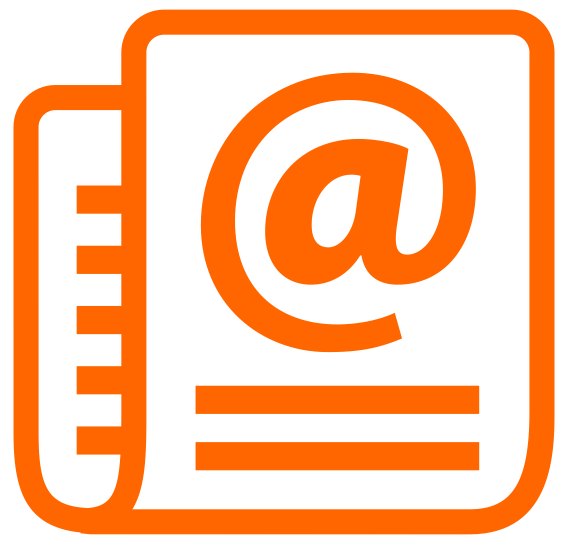
REKLAMA |
Litości za takich "redaktorów"...