

Analityka predykcyjna i optymalizacja utrzymania ruchu
Niska jakość produktów spowodowana przez awarie komponentów, zmniejszenie wydajności produkcji w wyniku długich przestojów - to problemy, które należą do przeszłości w erze sztucznej inteligencji i uczenia maszynowego. Poniżej zaprezentujemy jak można zoptymalizować konserwację utrzymania ruchu i jak to się przekłada na regularną produkcję.
Co oznacza optymalizacja utrzymania ruchu i dlaczego jest ona istotna?
Optymalizacja utrzymania ruchu obejmuje trzy sposoby usprawniania konserwacji urządzeń w zakładzie. Skraca się niegdyś czasochłonne i kosztowne procesy konserwacji remontów, oszczędzając tym samym pieniądze i środki. Jest to możliwe dzięki wczesnemu planowaniu prac konserwacyjnych. W ten sposób można w szczególności skrócić czas przestoju maszyn, co przekłada się na ograniczenie zakłóceń w produkcji.
Usprawnienie może także oznaczać - w zależności od systemu - optymalizację operacji nadmiarowych, która pozwala całkowicie wyeliminować awarie maszyn poprzez łączenie komponentów nadmiarowych na wczesnym etapie. Rezultatem są oszczędności wynikające z jednej strony z ograniczenia czasu przestoju, a z drugiej z możliwości przeprowadzenia remontu urządzeń w zakładzie zamiast kupna nowego komponentu. Istotną korzyścią jest również oszczędność czasu, gwarantowana dzięki szybszej dostępności regenerowanych komponentów, ponieważ klient nie musi już brać pod uwagę długiego czasu dostawy. Trzecim aspektem, który można zmodyfikować w obszarze utrzymania ruchu jest zastąpienie konserwacji cyklicznej działaniami w oparciu o faktyczny stan urządzenia. Dzięki temu operatorzy maszyn mogą przeprowadzać konserwację w sposób bardziej efektywny i opłacalny.
Zilustrujmy to na przykładzie:
Thomas jest kierownikiem ds. serwisu w ABC Metallurgy Group i wraz ze swoim zespołem odpowiada za płynność produkcji w fabryce w Monachium. Pięcioosobowy zespół serwisowy dysponuje wieloletnim doświadczeniem w dziedzinie hydrauliki, mechaniki i elektroniki istniejących maszyn.
Thomas jest obecnie zadowolony ze swoich pracowników: po tylu latach pracy częste przestoje są eliminowane tak szybko jak jest to możliwe poprzez identyfikację pojawiających się awarii, zamawianie części zamiennych i ich montaż. Jednak kierownik produkcji wywiera na nim presję, narzekając na pogarszającą się jakość produktów spowodowaną awariami komponentów, a także nieplanowanymi i długimi przestojami maszyn w trakcie konserwacji remontów. Kierownik produkcji może zaplanować z wyprzedzeniem tylko cykliczne, kwartalne przeglądy serwisowe, ale nieplanowane przestoje w czasie pomiędzy nimi stają się coraz częstsze i dłuższe, bo w zespole Thomasa chwilowo brakuje pracowników, a przyjęcie nowych specjalistów nie jest brane pod uwagę.
W przypadku wyłączenia zespół Thomasa otrzymuje informację, po czym dostępni pracownicy organizują się i badają maszynę. Po wykryciu usterki, co w najgorszym przypadku może zająć kilkanaście godzin, właściwe części zamienne są zamawiane u dostawcy. Dostawa trwa kilka tygodni, w zależności od dostępności elementów. W tym czasie na danej maszynie nie można kontynuować produkcji, co przekłada się na znaczne straty.
Ale Thomas zorganizował swój zespół w najlepszy możliwy sposób i nie zmieni niczego w kwestii dostawy części zamiennych, więc jak jeszcze może zoptymalizować procesy naprawcze?
Jakie wymogi stawia optymalizacja utrzymania ruchu?
Utrzymanie ruchu można zoptymalizować podejmując krótkotrwałe działania zależne od stanu maszyny. Potrzebny jest do tego system umożliwiający prowadzenie analiz prognozujących, na przykład za pomocą algorytmów uczenia maszynowego. Takie rozwiązania, jak np. narzędzia ODiN firmy Bosch Rexroth, pomagają operatorom maszyn w planowaniu prac konserwacyjnych na wczesnym etapie. Jest to jednak możliwe tylko poprzez łączenie maszyn lub systemów w celu gromadzenia i oceny danych. Wybiegająca w przyszłość analiza jest zatem możliwa tylko przy wykorzystaniu danych dotyczących maszyny.
Jak pozyskuje się dane do istotnych prognoz?
Maszyny, które mają być monitorowane muszą zostać w tym celu wyposażone w odpowiednie czujniki umożliwiające gromadzenie właściwych danych do analizy. Dane są zapisywane tymczasowo i wstępnie przetwarzane za pomocą oprogramowania IoT Gateway, a następnie umieszczane w chmurze. Tam przeprowadzana jest analiza zgromadzonych danych. Analiza ta jest wykorzystywana do przetwarzania złożonych wzajemnych powiązań, które człowiekowi jest trudno zrozumieć i przełożenia ich na informacje istotne dla osoby podejmującej decyzję. Ostatecznie, gdy system wykryje odstępstwo, wykwalifikowany pracownik diagnozuje stan maszyny i zaleca odpowiednie działania.
Jeśli w proces ten jest zaangażowany dostawca usług serwisowych, taki jak Bosch Rexroth, eksperci mogą przekazać zalecenia, a klient sam decyduje o ich wprowadzeniu. W zależności od typu umowy, zalecane działania są realizowane przez dostawcę usług serwisowych lub samodzielnie przez klienta.
Wszystkie te dane oraz doświadczenie zgromadzone w procesie analizy pomaga w ciągłym doskonaleniu narzędzia analitycznego. Im więcej danych udostępni się systemowi do „nauki“, tym bardziej staje się on „inteligentny“ i tym szybsze i bardziej precyzyjne decyzje można podejmować w przyszłości.
Jak optymalizacja jest widoczna w produkcji na co dzień
Jeśli dane dotyczące maszyny są gromadzone, analizowane przez system i oceniane przez eksperta, w przypadku umowy serwisowej (np. ODiN) osoba do kontaktu generuje zalecenia dla klienta. Klient może samodzielnie zadecydować o ich wprowadzeniu. Inne umowy dotyczące serwisu, takie jak umowa o zarządzaniu częściami zamiennymi, obejmująca części zamienne, którymi dysponuje dostawca usługi lub dostawę komponentu w ciągu maksymalnie 24 godzin, oferują firmie dodatkowe korzyści pozwalające w wykorzystać w pełni optymalizację utrzymania ruchu za pomocą analiz predykcyjnych. Pozwala to operatorowi maszyny przeprowadzać konserwację w oparciu o stan urządzeń, ograniczyć czas przestojów i zminimalizować zakłócenia w produkcji.
Jak Thomas wykorzystał optymalizację konserwacji w praktyce
Kierownik ds. produkcji wskazał Thomasowi rozwiązanie cyfrowe, usługę analiz predykcyjnych, które pomogą jemu i jego zespołowi w prowadzeniu prac konserwacyjnych. Thomas podchodzi jednak sceptycznie do zakresu, w jakim może to pozytywnie wpłynąć na jego pracę.
Z rozmowy z przedstawicielem Bosch Rexroth dowiedział się, że firma ta oferuje rozwiązanie w zakresie analityki predykcyjnej, wspomagające serwisowanie dostarczanych przez nią urządzeń hydraulicznych. Thomas, zainteresowany tą kwestią, spisał sobie zalety systemu.
ODiN od Bosch Rexroth - analityka predykcyjna
- Analiza danych maszyny za pomocą czujników - brama - chmura (ważne!)
- Właściwa organizacja zespołu
- Wczesne zamawianie części zamiennych, w chwili wykrycia błędów
- Błąd jest już wykryty przez system → możemy sprawdzić konkretną maszynę
- Krótsze czasy przestoju
- Większa wydajność pracy mojego zespołu
- Optymalne wykorzystanie wydajności
- Mniej zakłóceń w produkcji
To rozwiązanie znacząco odmieni codzienną pracę Thomasa i jego zespołu.
Po zastosowaniu odpowiednich czujników i ich przetestowaniu na systemach przez firmę Bosch Rexroth Thomas zaledwie dwa miesiące później otrzymał komunikat ostrzegawczy informujący o uszkodzeniu pompy hydraulicznej, które prawdopodobnie doprowadzi do jej całkowitej niesprawności w ciągu dwóch tygodni. Części zamienne zostały niezwłocznie zamówione w firmie Bosch Rexroth, a dwóm technikom zlecono przeprowadzenie naprawy w sobotę, osiem dni później. Pompę wymieniono w ciągu godziny, co oznacza, że produkcja została tylko nieznacznie zakłócona podczas weekendu.
ABC Metallurgy Group może w sposób wydajny i zoptymalizowany przeprowadzać remonty, co pozwala zaoszczędzić koszty i czas w przypadku przestojów, ograniczyć odpady podczas produkcji, a w dłuższej perspektywie zwiększyć konkurencyjność na rynku.
REKLAMA |
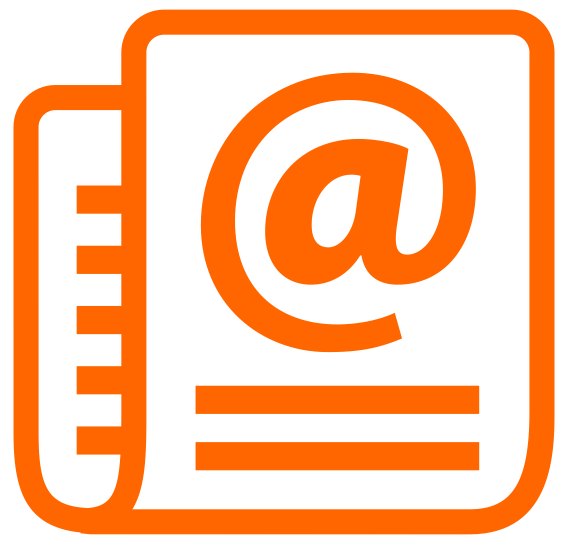
REKLAMA |