

Dozowanie płynów i miniaturyzacja sektora elektronicznego
Rozwój technologii z każdym rokiem nabiera coraz większego tempa. Miniaturyzacja inteligentnych modułów elektronicznych jest fascynującym zjawiskiem oferującym coraz większe możliwości.
Jeszcze kilka lat temu nie byliśmy w stanie wyobrazić sobie dostępnych funkcjonalności, które obecnie są standardem. Żeby się o tym przekonać, wystarczy porównać klasyczny telefon dotykowy dostępny w sklepach 10 lat temu i dzisiejsze smartfony. Wszystko za sprawą rozwoju technologii dozowania płynów i wiedzy na ten miniaturyzacji oraz odprowadzania ciepła podczas pracy eksploatowanych modułów.
Dozowanie płynów w miniaturyzacji modułów elektronicznych
Miniaturyzacja pozwala nam na wykorzystanie większej mocy obliczeniowej, mimo mniejszych rozmiarów podzespołów. Żeby było to możliwe, koniecznie należy sięgnąć po innowacyjne metody montażu, które zapewniają efektywną wentylację, regulację temperatury, ochronę przed uszkodzeniami mechanicznymi, drganiem itp. Dzięki temu możemy zaobserwować także rozwój montażu powierzchniowego, czyli np. conformal coatingu, underfill, dam & fill, zalewanie i uszczelki wylewane. Stosowanie takich preparaty jak kleje SMA, pasty termoprzewodzące, zalewy, uszczelniacze, smary i oleje nakładane, nigdy nie było tak wydajne, proste i czyste, jak teraz - tak technologię stosuje np. AMB Technic.
Warto zwrócić jednak uwagę na dość ciekawe sprzężenie zwrotne, które polega na doprecyzowaniu dozowania coraz bardziej skomplikowanych i zaawansowanych w obróbce materiałów. Pozwala ono na ograniczenie wymiarów i obniżenie kosztu jednostkowej operacji montażowej. Czy to znaczy, że odnotowujemy stały postęp i eliminację tzw. wąskich gardeł? Tak!
Problematycznym parametrem może być jednak wielkość serii. Produkcja niewielkiej ilości komponentów bywa w wielu przypadkach nieopłacalna. Wykorzystując jednak dokładną analizę wad i zalet konkretnej metody produkcji oraz konfiguracji procesu, można znaleźć rozwiązania zapewniające efektywność na zadowalającym poziomie.
Jak to zrobić? Wyróżniamy dwie podstawowe warstwy, w których szczegółowa analiza indywidualnego zapotrzebowania i ocena wydajności procesu produkcji są niezbędne. Należą do nich:
- warstwa automatyzacyjna;
- warstwa reologiczna.
W obydwu przypadkach warstwy podlegają zupełnie innym kryteriom oceny. Trzeba zatem podejść do tematu z pełnym profesjonalizmem, umiejętnościami i świadomością.
Dostępne technologie dozowania płynów
Wyróżniamy kilka poziomów zaawansowania procesu automatyzacji dozowania płynów. Do najpopularniejszych zaliczamy m.in.:
- Zaawansowane procesy dozowania in-line;
- Systemy in-line dostosowane do mniejszych zapotrzebowań;
- Roboty stolikowe i mało skomplikowane stacje robocze;
- Dyspensery ręczne.
Pierwszy, czyli najbardziej rozbudowany proces dozowania in-line to super wydajna metoda zapewniająca szybkość realizacji zadań i precyzję na najwyższym poziomie. Stosowana jest ona do nakładania np. klejów SMA lub wzmacniania układów BGA.
Systemy in-line dla mniejszych zapotrzebowań (jak sama nazwa wskazuje) są wykorzystywane wtedy, gdy nakład produkcyjny jest średniej wielkości. Przy największych zamówieniach wykorzystuje się ww. zaawansowane procesy dozowania in-line. Przy jeszcze mniejszych zleceniach roboty stolikowe, proste stacje robocze lub nawet dyspensery ręczne są najlepszym rozwiązaniem.
Doświadczony specjalista jest w stanie sprostać zamówieniu 20 tysięcy dawek płynów w ciągu jednego dnia. Roboty i mało skomplikowane systemy mają niewiele większą wydajność, lecz są w stanie zautomatyzować proste czynności. Pracownicy w tym czasie mogą zająć się innymi obowiązkami, co również poprawia efektywność pracy danej działalności lub zespołu.
REKLAMA |
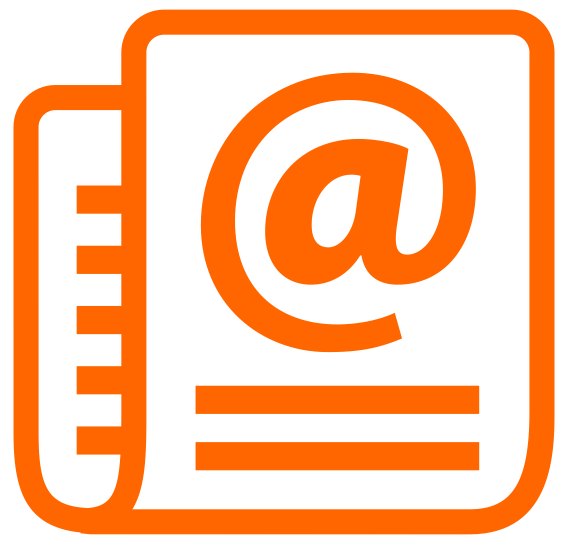
REKLAMA |