

Dlaczego warto wykonywać analizę pracy silnika jako część procedury konserwacyjnej?
Cztery kluczowe elementy umożliwiające zrozumienie wydajności silnika oraz przyczyn awarii.
Silniki elektryczne zmieniają energię elektryczną w mechaniczne siły obrotowe, które są „mięśniami” świata przemysłu. Mierzenie i analizowanie tych sił – mocy mechanicznej, momentu obrotowego i prędkości – oraz jakości energii elektrycznej jest niezwykle ważne w procesie oceny wydajności urządzeń obrotowych. Takie pomiary pomagają przewidzieć awarie i zapobiegają przerwom w pracy, a także pomagają szybko określić, czy wymagane są dodatkowe inspekcje w celu potwierdzenia otrzymanych wyników, np. testy wibracyjne, analiza wyrównania wału lub test izolacji.
Tradycyjnie uzyskanie dokładnych danych analitycznych dotyczących pracy silnika było związane z kosztownym procesem wyłączania urządzeń w celu montażu czujników mechanicznych. Prawidłowy montaż czujników mechanicznych był nie tylko bardzo trudny (a czasami niemożliwy) – same czujniki były często nieopłacalne i wprowadzały zmienne, które mogły pogorszyć ogólną wydajność systemu.
Nowoczesne narzędzia do analizy pracy silnika znacznie ułatwiają bezpośrednie rozwiązywanie problemów w działających silnikach elektrycznych poprzez uproszczenie procesu i zredukowanie liczby komponentów i narzędzi wymaganych do podejmowania ważnych decyzji związanych z konserwacją. Przykładowo nowe narzędzie do testowania jakości zasilania i analizowania pracy silników Fluke 438-II sprawia, że technicy mogą badać elektryczną i mechaniczną wydajność silników elektrycznych, a także oceniać jakość energii elektrycznej poprzez pomiary zasilania trójfazowego podawanego do silnika – bez użycia czujników mechanicznych.
Fluke 438-II
Oto CZTERY KLUCZOWE ELEMENTY umożliwiające zrozumienie ogólnej wydajności silnika i systemu:
1. Niska jakość energii elektrycznej ma bezpośredni wpływ na wydajność silnika
Anomalie zasilania, np. stany przejściowe, harmoniczne lub zachwianie równowagi mogą powodować znaczne uszkodzenia w silnikach elektrycznych. Anomalie zasilania, np. stany przejściowe i harmoniczne, mogą być szkodliwe dla pracy silnika. Stany przejściowe mogą powodować poważne uszkodzenia w izolacji silnika lub wyzwalać zabezpieczenia przeciwprzepięciowe w obwodach, co prowadzi do znacznych strat finansowych. Harmoniczne, które wytwarzają zakłócenia w napięciu i prądzie, mają podobny, negatywny wpływ i mogą prowadzić do wzrostu temperatury silników i transformatorów, co może spowodować przegrzewanie się lub awarię. Poza zmianami harmonicznych może dochodzić do zachwiania równowagi napięcia i prądu, co jest często główną przyczyną podwyższonej temperatury silnika i długoterminowego zużycia, w tym spalonych uzwojeń. Używając trójfazowych pomiarów na wejściu silnika, technicy mogą zgromadzić obszerne dane, które pomagają w określeniu ogólnego stanu i jakości energii elektrycznej, a przez to w lepszym rozwiązywaniu problemów przyczyniających się do niskiej wydajności silnika.
2. Wpływ momentu obrotowego na ogólną wydajność i sprawność
Moment obrotowy jest ilością siły obrotowej wytworzonej przez silnik i przekazanej do napędzanego obciążenia mechanicznego. Prędkością określa się szybkość obrotu wału silnika. Moment obrotowy silnika, mierzony w funtach na stopę (lb/ft) lub niutonometrach (Nm), jest pojedynczą, najważniejszą zmienną charakteryzującą natychmiastową wydajność mechaniczną. Tradycyjnie moment obrotowy mierzono za pomocą czujników mechanicznych. Obecnie tester Fluke 438-II oblicza moment obrotowy za pomocą parametrów elektrycznych (wartość chwilowa napięcia i prądu) w połączeniu z danymi z tabliczki znamionowej silnika. Pomiar momentu obrotowego może zapewnić bezpośredni wgląd w stan silnika, jego obciążenie oraz proces.
Praca silnika z momentem obrotowym określonym w specyfikacji zapewnia niezawodne działanie w dłuższym czasie i minimalizuje koszty związane z konserwacyjną.
3. Dane znamionowe silnika i przewidywane osiągi
Silniki klasyfikuje się według wartości znamionowych NEMA (National Electrical Manufacturers Association) i IEC (International Electrical Commission). Klasyfikacje te zawierają kluczowe parametry elektryczne i mechaniczne, np. znamionową moc silnika, maksymalny prąd obciążenia, prędkość silnika i nominalną wydajność przy pełnym obciążeniu oraz opisują ogólne przewidywane osiągi silnika w normalnych warunkach pracy. Współczesne narzędzia analizy pracy silnika korzystają z zaawansowanych algorytmów i mogą porównywać trójfazowe pomiary elektryczne z wartościami znamionowymi, co umożliwia wgląd w wydajność silnika w warunkach z faktycznym obciążeniem. Różnica między pracą silnika zgodnie ze specyfikacją producenta a jego działaniem poza określonymi parametrami ma ogromne znaczenie.
Uruchamianie silników w warunkach przeciążenia mechanicznego powoduje nadmierne obciążenie komponentów silnika, np. łożysk, izolacji i połączeń, co prowadzi do spadku wydajności i skraca żywotność urządzenia.
4. Wydajność silnika ma bezpośredni wpływ na oszczędność energii
Obecnie przemysł nieustannie stara się zredukować zużycie energii i zwiększyć wydajność silników poprzez „zielone” inicjatywy. W wielu krajach te inicjatywy stają się przepisami prawa. Jedno z ostatnich badań wykazało, że silniki zużywają 69% całej energii elektrycznej wykorzystywanej w przemyśle oraz 46% całej energii elektrycznej w kontekście globalnym.
Identyfikując silniki o niskiej wydajności lub te, które uległy awarii, a następnie naprawiając lub wymieniając je, można kontrolować zużycie energii i efektywność pracy. Analiza jakości energii elektrycznej i pracy silników zapewnia odpowiednie dane umożliwiające zidentyfikowanie i potwierdzenie nadmiernego zużycia energii oraz powodów niskiej wydajności. Ponadto ta sama analiza może zweryfikować usprawnienia po naprawie lub wymianie. Do tego poznanie stanu silników i możliwość interwencji przed awarią redukuje narażenia na potencjalne wypadki zagrażające bezpieczeństwu lub środowisku.
Dane dotyczące jakości energii elektrycznej i pracy silnika nie są statyczne. Zmiana warunków oznacza zmianę pomiarów. Awarie silników zostały zidentyfikowane przez 75% ankietowanych w badaniu przemysłowym jako przyczyna 1-5 dni przestojów w pracy zakładu (rocznie). 90% ankietowanych stwierdziło, że awarie silników o mocy ponad 50 KM były przewidywane na mniej niż miesiąc przed awarią (36% stwierdziło, że ostrzeżenie o awarii pojawiało się na mniej niż dzień przed jej wystąpieniem). Zebranie podstawowych danych jest pierwszym krokiem na drodze do programu konserwacji prognostycznej lub zapobiegawczej. Zacznij od zbierania dokładnych odczytów podstawowych o pracy silników, a następnie podejmij kolejne kroki i śledź trendy. Aby osiągnąć najlepsze rezultaty, pomiarów powinno dokonywać się w stałych, powtarzalnych warunkach roboczych (najlepiej o tej samej porze dnia). Dzięki temu można dokonać właściwych porównań. Taką metodologię można stosować wobec danych dotyczących jakości energii elektrycznej (harmoniczne, zachwianie równowagi, napięcie itp.) oraz pracy silnika (moment obrotowy, prędkość, moc mechaniczna, wydajność).
Nowy przyrząd do testowania jakości zasilania i analizowania pracy silników Fluke 438-II ułatwia zbieranie podstawowych danych bezpośrednio z pracujących silników i wykrywanie usterek mechanicznych lub elektrycznych bez potrzeby wyłączania systemu z obiegu pracy. Dodając do zestawu narzędzi urządzenie do analizy elektrycznej i mechanicznej silników elektrycznych, możesz zagwarantować odpowiednie dane, które pomogą utrzymać ciągłość pracy zakładu.
REKLAMA |
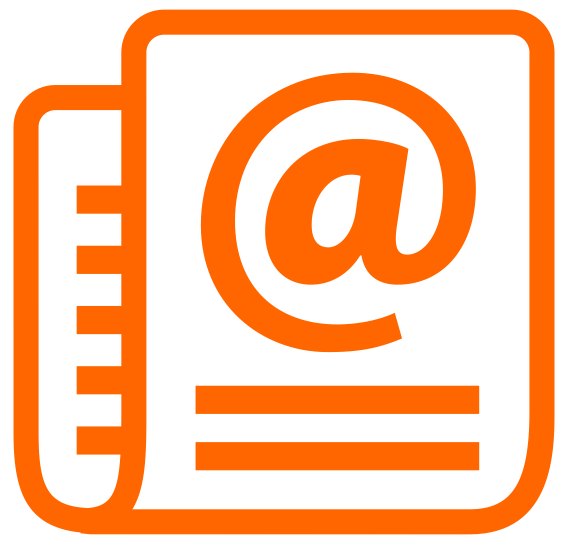
REKLAMA |